Maximo Inventory Management: Streamlining Efficiency
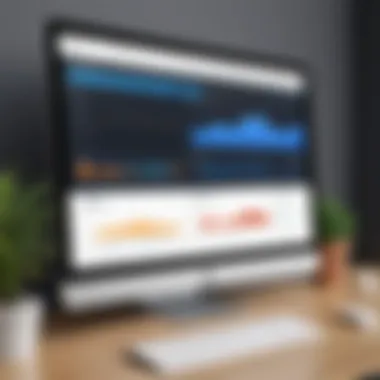
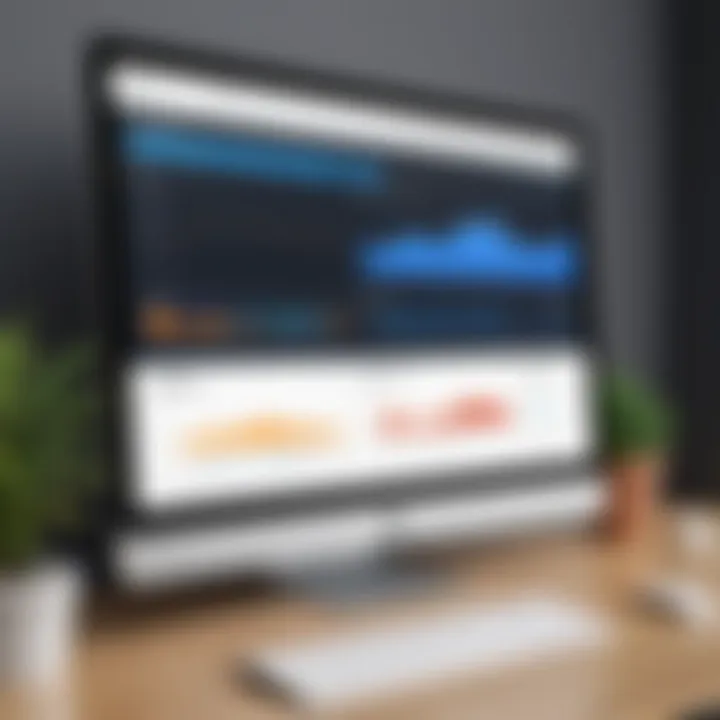
Intro
Maximo Inventory Management is pivotal for both small and large organizations aiming to optimize their inventory processes. As supply chains grow complex, the need for effective inventory control becomes paramount. This section sets the groundwork for understanding how Maximo facilitates this aspect of business operations. Companies that effectively manage inventory can contribute to cost savings, better customer satisfaction, and overall improved operational efficiency.
In this exploration, we will cover various aspects including its core functionalities, benefits, and how it integrates with existing business processes. The knowledge gained here will help in making informed decisions on implementing Maximo's capabilities effectively, ultimately leading to sustainable business growth.
Software Overview
Maximo's inventory management software is designed to streamline inventory processes. It offers a rich array of features and technical specifications tailored for diverse organizational needs.
Software Features
Maximo provides various key features that enhance its utility in inventory management:
- Real-time Tracking: Monitor inventory levels continuously, reducing the chances of stockouts or overstocking.
- Automated Replenishment: Automatically trigger orders when stock levels fall below predefined thresholds, ensuring optimal inventory levels.
- Mobile Access: Users can access Maximo's functions on-the-go via mobile devices, increasing accessibility and flexibility.
- Reporting and Analytics: Detailed reporting tools provide insights into inventory turnover rates and stock trends, empowering users to make data-driven decisions.
- Integration Capabilities: Maximo can seamlessly integrate with other enterprise systems, maintaining data consistency across the organization.
Technical Specifications
Understanding the technical aspects can clarify how Maximo meets diverse user needs:
- Deployment Options: Available in both cloud and on-premises configurations, providing flexibility based on organizational preferences.
- Supported Platforms: Compatible with various operating systems, including Windows, Linux, and mobile platforms.
- Scalability: Designed to grow with your business, Maximo can handle increasing volumes of data and user activity.
- Security Features: Robust security measures ensure data integrity and compliance with industry standards.
Peer Insights
Gaining insight from users can greatly inform potential adopters about the real-world applications of Maximo. Here, we provide a synthesis of user experiences along with the software’s strengths and drawbacks.
User Experiences
Users have shared varied feedback about how Maximo affects their inventory management practices. Many report that the real-time tracking feature is a game changer, allowing for swift responses to inventory demands. Others appreciate the seamless integration with their existing systems, which has simplified many workflows.
Pros and Cons
Evaluating the pros and cons is crucial before committing to any software:
Pros:
- Enhanced Efficiency: Streamlines processes, leading to significant time savings.
- Cost-saving Potential: Reduces excess inventory and associated costs through effective management strategies.
- User-Friendly Interface: Many users find Maximo’s interface intuitive, facilitating ease of use across teams.
Cons:
- Initial Setup Complexity: Setting up the system can be challenging and requires a dedicated resource.
- Cost Considerations: For smaller organizations, the investment could be substantial, necessitating careful cost-benefit analysis.
"Adopting Maximo has transformed our inventory workflow, but like any robust tool, it requires an investment in time and resources to maximize its potential."
– User Testimonial
Intro to Maximo Inventory
Maximo Inventory Management holds a significant role in enhancing the overall efficiency and effectiveness of organizational operations. This section serves as an entry point into understanding the integral aspects and functionalities of Maximo in the realm of inventory. The ability to manage inventory effectively can have profound implications on resource allocation, operational costs, and customer satisfaction.
Background of Maximo Software
Maximo, developed by IBM, has evolved over time to become a leading enterprise asset management tool. It originated as a simple asset management system, but its capabilities have expanded to encompass extensive inventory management features. The software is designed to assist organizations in tracking and managing assets, including materials and products, throughout their lifecycle. Moreover, Maximo is known for its flexibility to adapt to different business needs, allowing for integration with existing systems. This adaptability makes it a preferred choice for various industries, from manufacturing to healthcare.
Importance of Inventory Management
Effective inventory management is not merely a logistical concern; it is a strategic imperative. Teams that utilize Maximo for inventory management benefit from precise tracking and control of stock levels, which in turn leads to several advantages:
- Improved Visibility: Organizations achieve better visibility into their inventory status, allowing for informed decision-making.
- Cost Reduction: By minimizing excess stock and efficient order placement, operational costs are significantly reduced.
- Enhanced Service Levels: Accurate inventory records improve the ability to meet customer demands promptly, thereby enhancing satisfaction.
- Risk Management: Tracking inventory helps identify slow-moving items and potential shortages, allowing businesses to mitigate risks proactively.
Given these benefits, understanding the fundamentals of Maximo Inventory Management becomes crucial for enterprises aiming to thrive in a competitive environment.
Core Components of Maximo Inventory
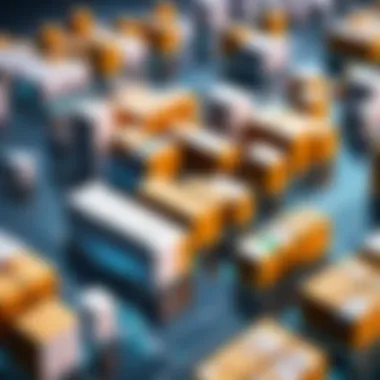
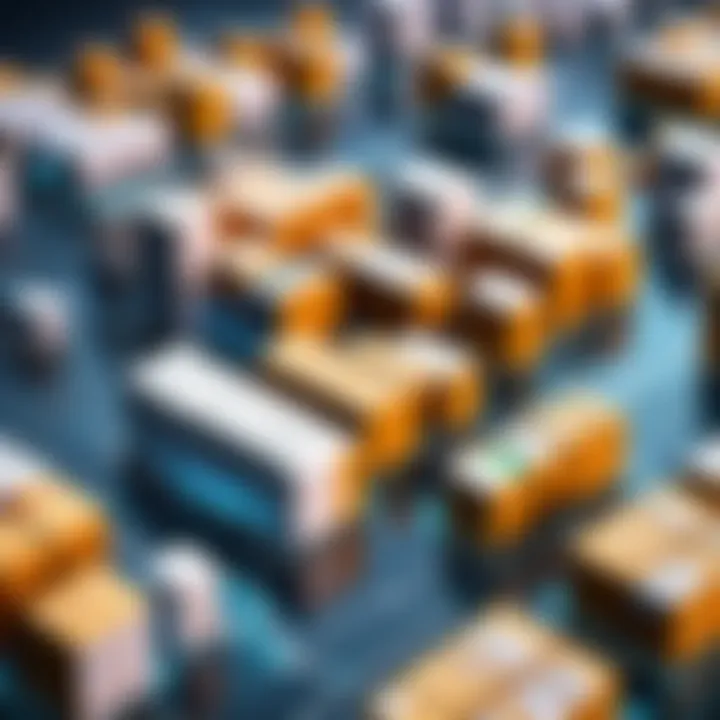
Understanding the core components of Maximo Inventory is essential for any organization aiming to optimize its asset management and inventory control. This section delves into the primary elements that define Maximo's inventory capabilities, explaining how they contribute to better operational functionality and improved decision-making. The seamless integration of these components helps businesses maintain their assets efficiently, thus enhancing productivity.
Inventory Tracking Capabilities
Inventory tracking is a critical function within Maximo Inventory. It enables companies to have real-time visibility into their inventory status. This functionality allows users to monitor stock levels, expiration dates, and product movements. With an effective tracking system, organizations can avoid stockouts, overstocks, and waste.
Key aspects of tracking capabilities include:
- Real-time Data: Maximo provides up-to-date information about inventory levels. This ensures that decisions are based on current data.
- Barcode Scanning: Integration of barcode technology helps in the accurate recording of items entering or leaving inventory. This reduces human error and speeds up the process.
- Reporting and Analysis: The ability to generate custom reports allows businesses to analyze inventory trends over time. This insight is crucial for effective planning and strategic decisions.
Overall, the inventory tracking capabilities within Maximo play a pivotal role in enhancing inventory accuracy and efficiency.
Asset Management Integration
Another essential component of Maximo Inventory is its integration with asset management systems. By linking inventory management with asset oversight, organizations can ensure that they have the right assets available when needed. This integration fosters a holistic view of operations.
The benefits include:
- Improved Asset Utilization: Companies can track which assets are in use and their corresponding inventory needs, which leads to smarter allocation of resources.
- Lifecycle Management: Maximo helps manage the entire lifecycle of an asset—from acquisition to disposal. This ensures that organizations maximize value from each asset.
- Streamlined Processes: By combining inventory and asset management, businesses can streamline operations, reducing redundancies and improving overall efficiency.
In summary, the integration between inventory tracking and asset management provides a robust framework for organizations seeking to enhance their operational capabilities. Both components work together to create a cohesive system that is vital for managing resources effectively.
"Efficient inventory management is an investment in the future of any organization. Maximo offers the tools necessary to realize this potential through its core components."
Functionalities of Maximo Inventory Management
Maximo Inventory Management plays a pivotal role in streamlining operations and enhancing productivity in various business processes. The functionalities offered by Maximo provide a framework that facilitates effective inventory control. Understanding these functionalities helps organizations utilize their resources efficiently and respond promptly to changing demands in the market. Effective implementation of these functionalities can lead to cost savings and increased operational efficiency, making it essential for IT and software professionals to grasp their intricacies.
Stock Level Monitoring
Stock level monitoring is one of the cornerstone features within Maximo Inventory Management. It allows businesses to keep real-time track of their inventory levels, ensuring that stock is available when needed. This feature mitigates the risk of stockouts or overstocking, which can lead to financial waste and inefficiencies.
By utilizing various tools within Maximo, businesses can set minimum and maximum stock thresholds. Alerts can be configured to notify users when stock levels approach these limits. This proactive monitoring not only optimizes stock management but also enhances service levels, as items can be readily available for operations without excess tying up capital in inventory.
- Key Benefits of Stock Level Monitoring:
- Real-time visibility of inventory levels.
- Enhanced decision-making based on accurate data.
- Reduction in operational disruptions due to inventory shortages.
Automated Replenishment Processes
Automated replenishment processes in Maximo Inventory Management ensure continuous availability of stock without the need for manual intervention. This feature utilizes algorithms to forecast inventory needs based on historical data and usage patterns.
The automation can help determine reorder points for products, making procurement more streamlined. It can analyze inventory turns and suggest optimal order quantities. This is particularly useful for companies with high-volume inventory turnover or seasonal demands, where fluctuations are frequent.
- Advantages of Automated Replenishment:
- Minimizes excess inventory and associated holding costs.
- Saves time by reducing manual ordering processes.
- Improves supplier management and collaboration.
Custom Reporting Features
Custom reporting features within Maximo allow businesses to analyze their inventory data comprehensively. Users can create tailored reports that focus on various aspects of inventory management, such as demand trends, stock levels, and order histories.
These reports are invaluable for strategic planning and operational assessments. By identifying patterns and areas for improvement, organizations can make informed decisions that lead to enhanced resource allocation and better financial performance.
- Highlights of Custom Reporting Features:
- Flexibility to create reports that meet specific business needs.
- Ability to analyze data over time to spot trends and anomalies.
- Enhanced visibility into inventory-related KPIs, promoting accountability.
Ultimately, the functionalities embedded within Maximo Inventory Management provide an integrated approach to managing inventory more effectively. Businesses that leverage these capabilities can experience improved operational efficiency and reduced costs as a direct outcome of well-informed inventory practices.
Benefits of Using Maximo for Inventory Management
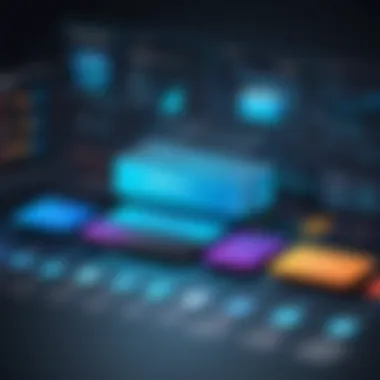
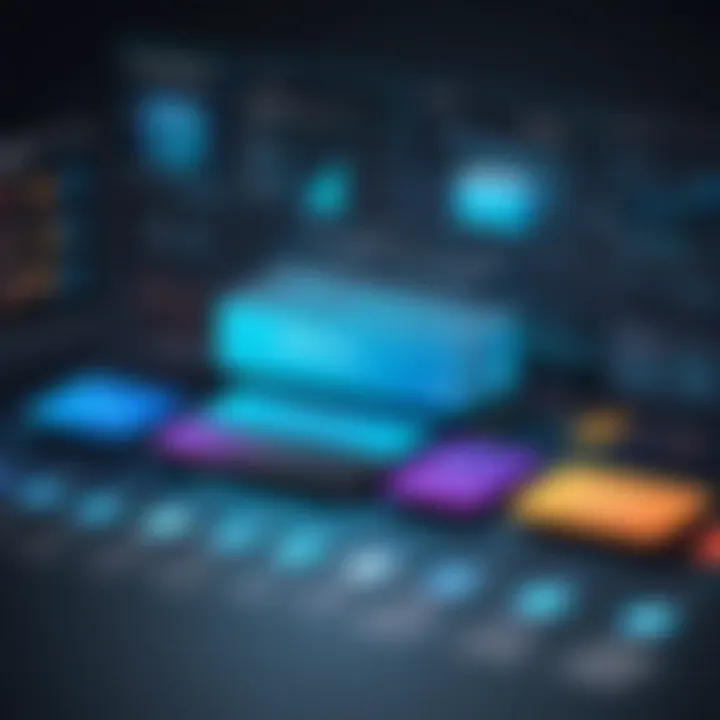
Maximo Inventory Management offers various advantages that significantly impact business operations. Understanding these benefits is crucial for organizations looking to optimize their inventory processes. By using Maximo, businesses can streamline operations, enhance efficiency, and reduce costs associated with inventory management. Here, we explore two key benefits: enhanced operational efficiency and reduced operational costs.
Enhanced Operational Efficiency
Operational efficiency is the backbone of any successful inventory management system. Maximo delivers this through its comprehensive inventory tracking capabilities.
With Maximo, organizations gain real-time visibility into their inventory levels. This transparency helps businesses avoid stock-outs or overstock situations. By implementing automated processes, users can reduce manual tasks, minimizing the risk of errors. The system features tools for monitoring stock levels, issuing alerts for low inventory, and facilitating timely replenishment.
Moreover, Maximo integrates seamlessly with asset management. By aligning inventory data with assets, businesses can optimize the lifecycle of inventory items. This integration supports better decision-making, as users can analyze inventory data alongside asset performance. This way, resources are allocated more judiciously, fostering a more efficient operational environment.
"Integrating asset management with inventory tracking is crucial for informed decision-making."
Additionally, Maximo offers customizable reporting features. Users can generate specific reports that provide insights into inventory trends and performance metrics. This data-driven approach allows organizations to adjust strategies based on empirical evidence rather than guesswork, further enhancing operational efficiency.
Reduced Operational Costs
Reducing operational expenses is fundamental to maintaining profitability. Maximo's inventory management capabilities can lead to significant cost savings for businesses. The first area of cost reduction is through improved inventory turnover. By implementing automated replenishment processes, companies can avoid holding excess inventory, which occupies valuable warehouse space and ties up capital.
Furthermore, accurate inventory tracking minimizes the risk of lost or misplaced items. With every item accounted for, companies reduce waste associated with expired or obsolete stock. This leads to more efficient allocation of resources, decreasing the need for frequent purchasing cycles, and thus lowering procurement costs.
Training and user adoption also factor into cost considerations. Maximo is designed with user-friendly interfaces, which means less time required for training employees. This not only speeds the implementation process but also reduces ongoing training costs associated with user retention.
In summary, businesses that leverage Maximo for their inventory management needs can see marked improvements in both operational efficiency and cost reduction. The integration of technology with inventory practices ultimately leads to streamlined operations, better decision-making, and savings that positively affect the bottom line.
Challenges in Maximo Inventory Implementation
Implementing Maximo Inventory Management comes with a set of challenges that organizations must navigate to utilize its full potential. Understanding these obstacles is crucial, as they can significantly influence the outcomes of the deployment and long-term effectiveness of the system. Recognizing user adoption and data migration issues are critical components of this discussion. These topics shed light on common pitfalls that affect performance and overall user satisfaction.
User Adoption Issues
User adoption is one of the foremost challenges in implementing Maximo Inventory Management. Successful implementation demands not just technical proficiency but also a commitment from users to embrace the new system. One major factor affecting adoption is the resistance to change; if employees are accustomed to a particular workflow or software system, they may feel reluctance towards adjusting to a different approach.
Training plays a vital role here. Organizations must provide comprehensive training programs that not just educate users about how to navigate Maximo but also emphasize the benefits it brings. Users need to see clear advantages in their daily tasks, such as improved efficiency or reduced workloads. Inadequate user training can lead to confusion and frustration, hindering the overall success of the system.
Some measures to enhance user adoption include:
- Hands-on training sessions tailored to the needs of different user groups.
- Establishing a feedback loop where users can express concerns and suggest improvements, thus fostering a sense of ownership.
- Leadership support to champion the new system, promoting a positive attitude towards embracing change.
Overcoming user adoption issues is essential for maximizing the value derived from Maximo Inventory Management.
Data Migration Difficulties
Another significant challenge lies in data migration. Transitioning data from existing systems to Maximo can be fraught with difficulties. Data integrity and accuracy are paramount. If data is lost, corrupted, or improperly migrated, it could undermine the entire purpose of implementing a sophisticated inventory management system.
The following aspects of data migration must be critically assessed:
- Data mapping: Careful mapping of existing data fields to their corresponding fields in Maximo is essential. Any misalignment can lead to data inconsistency.
- Data cleansing: Before migration, organizations should cleanse the data to remove duplicates and errors. This step is crucial to ensure only high-quality data is imported into the new system.
- Testing and validation: After migration, testing is necessary to confirm that data integrity is maintained. Validating the accuracy of migrated data will help identify issues early in the process.
Without addressing these challenges effectively, companies may face interruptions in operations and reduced productivity.
Case Studies of Maximo Inventory Implementation
Understanding the practical application of Maximo Inventory Management is essential for IT professionals and business leaders alike. Case studies provide real-world insights into how organizations deploy this software. They illuminate operational challenges, reveal pathways to success, and guide others considering implementation. By examining these scenarios, stakeholders can gather valuable information regarding best practices and potential pitfalls.
Success Stories
Success stories showcase effective implementations of Maximo Inventory within diverse industries. For instance, a large manufacturing firm improved their inventory accuracy by 30% after integrating Maximo solutions. This specific case emphasized how automated tracking and real-time data analysis can lead to efficient resource utilization. Another example involves a healthcare provider who streamlined their supply chain operations with Maximo Inventory, resulting in reduced delivery times and improved patient care outcomes. The synthesis of these experiences illustrates the transformative potential of Maximo in enhancing operational performance.
- Improved Accuracy: Increased inventory accuracy leads to better decision-making.
- Efficiency Gains: Time saved in inventory management translates into cost savings.
- Enhanced Customer Satisfaction: Reliable inventory management fosters trust and loyalty among customers.
Case studies highlight the tangible benefits of adopting Maximo Inventory, serving as a roadmap for prospective users.
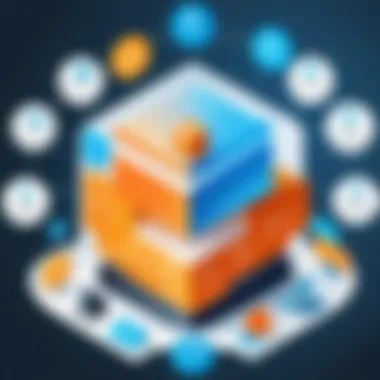
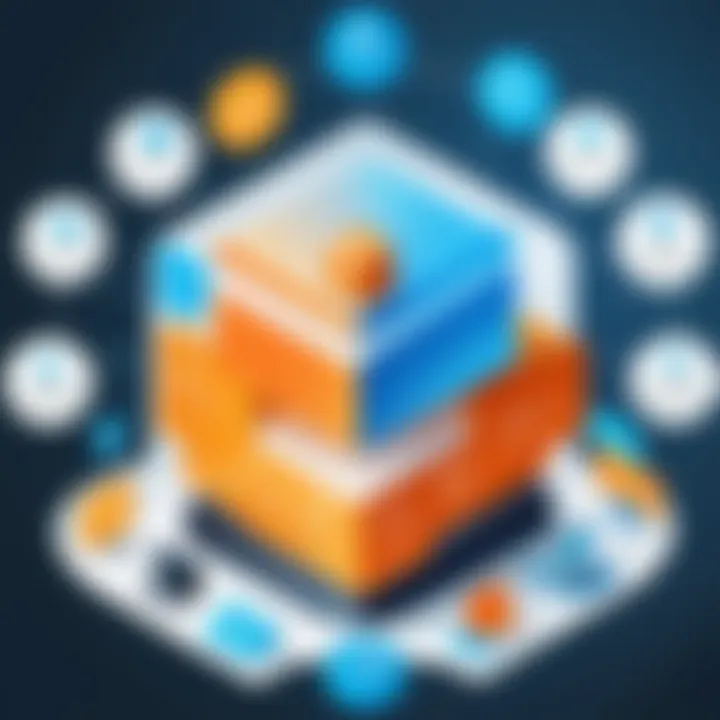
Lessons Learned
Every implementation, regardless of success, yields lessons that are critical for future endeavors. One common challenge reported involves user resistance to the software. In several organizations, team members were hesitant to adapt to the new system, which resulted in initial setbacks. Training programs became integral to overcoming this issue. Another lesson learned involves the importance of data integrity prior to migration. Some companies faced significant difficulties because they had not adequately cleansed their existing data. This experience highlights the necessity for proper planning and execution.
Key lessons drawn from case studies include:
- Engagement is Key: Involve all levels of staff early in the implementation process.
- Data Preparation: Clean, accurate data is fundamental for successful migration.
- Ongoing Training: Continuous education helps maintain system efficacy and user engagement.
By analyzing various case studies, organizations can create a framework that increases their chances of success in implementing Maximo Inventory Management. Ultimately, a careful review of successes and failures provides a comprehensive view of the implications and considerations surrounding this powerful tool.
Maximo Inventory and Industry Standards
In today's complex business environment, ensuring that inventory management aligns with industry standards is vital. Maximo provides a framework that helps businesses meet these standards effectively. Industry standards dictate not only compliance but also best practices that enhance operational efficiency. By employing Maximo for inventory management, organizations can align their processes with these standards and gain a competitive edge.
Compliance Requirements
Compliance is a critical aspect of inventory management. Different industries have specific regulatory requirements that must be adhered to, such as health regulations in pharmaceuticals or environmental standards in manufacturing. Using Maximo helps organizations maintain these compliance requirements by integrating necessary protocols into their inventory processes. The software offers features that enable traceability, reporting, and documentation, alleviating the burden of regulatory audits.
For example, a company in the food industry must ensure that it follows safety regulations that vary by region. With Maximo, it can track the movement of ingredients, ensuring that any recalls can be executed promptly. Similarly, compliance with ISO standards is also achievable with well-documented inventory practices provided by Maximo.
Best Practices in Inventory Management
Integrating industry standards into inventory management through Maximo facilitates adoption of best practices. These practices not only improve operational workflows but also reduce costs and increase accuracy. To achieve optimal inventory management, consider the following best practices:
- Continuous Training: Ongoing education for employees about Maximo features ensures that they utilize the system to its full potential.
- Regular Audits: Frequent evaluations of inventory accuracy can identify discrepancies early, allowing corrective actions to be taken.
- Real-Time Data Analysis: Utilizing Maximo's data analytics capabilities aids in making informed decisions regarding stock levels and purchasing strategies.
By adhering to these practices, businesses can ensure their inventory management processes not only comply with industry standards but also operate efficiently, leading to improved service levels and customer satisfaction.
Ensuring compliance with industry standards is not just about following rules; it's about establishing a framework for operational excellence and continuous improvement.
Future Trends in Inventory Management with Maximo
The future of inventory management is evolving rapidly, and Maximo is at the forefront of this transformation. Understanding future trends is critical for organizations looking to enhance their operational capabilities and maintain a competitive edge. Key elements such as technological advancements and the integration of artificial intelligence offer significant benefits that businesses must consider.
Advancements in Technology
Technology continues to reshape the landscape of inventory management. New tools and systems are being developed to simplify processes and improve accuracy. For instance, Internet of Things (IoT) devices allow for real-time monitoring of inventory levels, providing businesses with instant data to make informed decisions. Automation tools can streamline repetitive tasks, thus saving time and reducing errors.
Emerging technologies such as blockchain also offer the potential for increased transparency and security in inventory processes. These advancements facilitate better collaboration between suppliers and customers, leading to improved trust and efficiency in operations. Organizations leveraging these technologies can expect to see enhancements in data accuracy, reporting, and overall inventory management effectiveness.
Impact of Artificial Intelligence
Artificial intelligence plays a pivotal role in the future of inventory management. AI-driven analytics tools can predict inventory needs based on historical data and trends, allowing businesses to optimize stock levels. This predictive capability reduces the risk of overstocking or stockouts, which can impact an organization's bottom line.
Incorporating machine learning algorithms enables systems to learn from past behaviors, improving decision-making over time. Additionally, AI can automate ordering processes and enhance supplier relationship management, further streamlining operations. Businesses adopting AI tools in Maximo can expect smarter inventory management that adapts to changing market conditions.
"Utilizing AI in inventory management is no longer an option. It is a necessity for staying relevant and competitive in today’s market."
Organizations looking to the future must stay informed about these trends and actively incorporate these technologies into their inventory strategies. By doing so, they can anticipate market changes and better meet customer demands.
Ending and Recommendations
The conclusion of this article serves to encapsulate the essence of Maximo Inventory Management and offer a roadmap for best practices to consider moving forward. The intricate structure of Maximo's software emphasizes not just the capabilities of inventory management, but also the integration with broader operational frameworks. Understanding the nuances can empower businesses to make informed decisions that support their unique needs.
Summary of Key Insights
Maximo Inventory Management presents several crucial insights that should not be overlooked:
- Seamless Integration: It effectively integrates with asset management systems, providing a unified solution for tracking both inventory and assets. This creates an environment where data is accessible and actionable.
- Operational Efficiency: Through features such as stock level monitoring and automated replenishment, Maximo can significantly reduce manual errors and optimize inventory levels.
- Custom Reporting: The ability to create tailored reports provides insights into inventory usage patterns and informs more strategic planning.
- Challenges to Navigation: However, businesses must also be aware of the challenges presented, including user adoption issues and data migration hurdles. Addressing these components upfront can make the implementation process smoother.
"A well-planned approach in deploying Maximo can mitigate risks and enhance profitability."
Final Recommendations for Users
To maximize the utility of Maximo Inventory Management, the following recommendations are key:
- Thorough Training: Invest in comprehensive training programs for users to facilitate smoother transitions and enhance user adoption rates. Ensuring that staff are comfortable navigating Maximo will unlock its potential.
- Pilot Programs: Consider running pilot programs before full deployment. This approach enables businesses to identify and address potential pitfalls.
- Regular Reviews: Schedule periodic evaluations of the inventory management processes. This helps to adapt to changing business needs and technology advancements.
- Collaboration: Foster collaboration among departments. Maximo’s full benefits are realized when teams work together, leveraging the integrated data effectively.
- Feedback Mechanisms: Create feedback channels for users to express their experiences and suggest improvements in processes and functionalities.