Exploring CAD, CAM, and PLM Interconnections
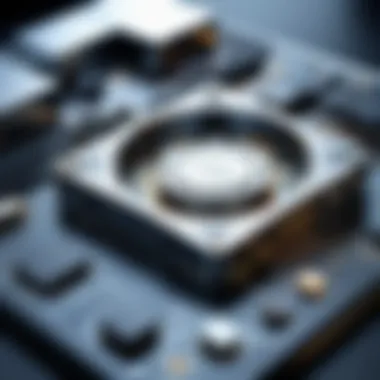
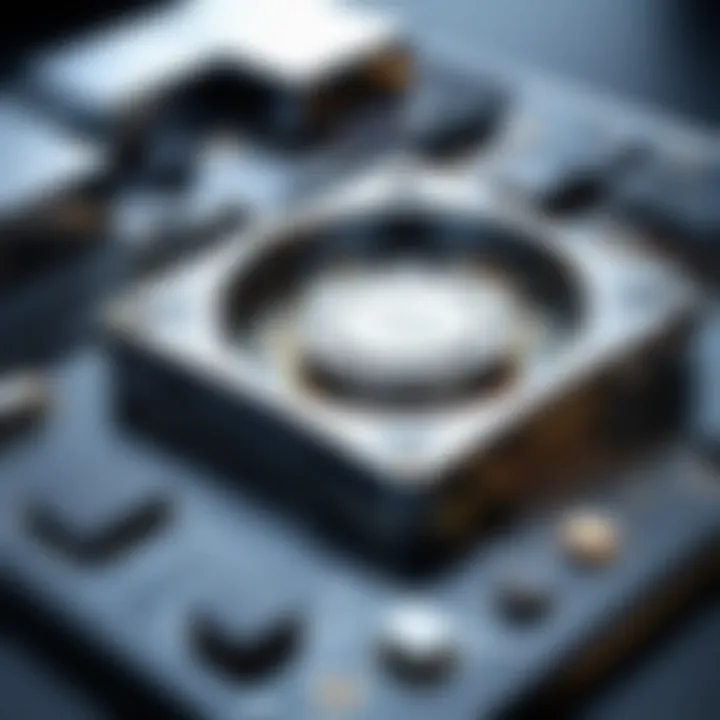
Intro
In today's fast-paced and intricately connected world of manufacturing and design, the integration of Computer-Aided Design (CAD), Computer-Aided Manufacturing (CAM), and Product Lifecycle Management (PLM) has emerged as a necessity. Each of these areas serves a specific role in the product development process, yet they are deeply interdependent, making their collaborative use essential to achieving efficiency and innovation. This article presents a detailed examination of how CAD, CAM, and PLM function individually and collectively, revealing their importance in the landscape of modern industrial practices.
The exploration will begin with a look at each domain’s functionalities. Following this, user experiences will provide insights into the practical implications of these technologies. The aim is to illustrate how the merging of these realms enhances operational workflows, drives product quality, and ultimately leads to more agile manufacturing environments.
Software Overview
Software Features
Computer-Aided Design (CAD) is predominantly focused on creating detailed drawings, specifications, and models. Tools like AutoCAD and SolidWorks provide features that enable designers to bring their visions to life through precision and customization. CAD systems not only support 2D designs but also facilitate intricate 3D modeling, making them indispensable to engineers and architects.
Computer-Aided Manufacturing (CAM) extends these capabilities into the realm of production. Systems such as Mastercam and Fusion 360 automate the machining processes. They convert CAD designs into machine instructions, optimizing cutting paths and manufacturing strategies. This efficiency reduces production time while maintaining accuracy, which is crucial for high-volume manufacturing.
Product Lifecycle Management (PLM) encompasses the management of a product's entire lifecycle, from inception to disposal. It integrates data, processes, and systems. Software like PTC Windchill facilitates collaboration across departments, ensuring that every stage of the product's development is documented and managed effectively. PLM fosters communication between CAD and CAM, creating unified data architectures that enhance decision-making.
Technical Specifications
When exploring the technical specifications of these systems, several aspects come into play:
- Interoperability is key. CAD and CAM software must communicate seamlessly, utilizing data formats such as STEP or IGES to ensure that designs can be faithfully translated into manufacturing processes.
- Scalability allows these systems to grow alongside a business. Solutions need to adapt irrespective of whether a company is a small startup or a large enterprise.
- Cloud capabilities have become increasingly common. This allows for real-time collaboration and access to tools from anywhere, streamlining workflows.
Peer Insights
User Experiences
Professionals using CAD, CAM, and PLM software often report varied experiences. Those in engineering appreciate the precision afforded by CAD tools. They note that features like parametric modeling can reduce design error rates significantly, which is crucial in maintaining high standards.
In manufacturing, CAD to CAM integration is praised for its efficiency. Users express that it lessens manual intervention, allowing machines to run autonomously with less risk. This synergy translates into substantial cost savings over time.
Pros and Cons
While the integration of CAD, CAM, and PLM presents numerous advantages, there are also challenges that users experience:
Pros:
- Improved efficiency and speed in product design and manufacture.
- Enhanced collaboration across teams through integrated systems.
- Higher quality products due to reduced errors through automated systems.
Cons:
- Initial high investment costs can be a barrier for many small businesses.
- The learning curve for complex systems might discourage some users.
- Compatibility issues often arise between different software solutions, complicating integration.
"In the essence of modern engineering, understanding the nuanced interdependence of design, production, and lifecycle management is paramount for sustained competitive advantage."
The discussion surrounding CAD, CAM, and PLM is crucial for professionals navigating today's manufacturing environment. Their interconnected nature not only enhances operational efficiency but also paves the way for innovative product development that can respond dynamically to market needs.
Prelims to CAD, CAM, and PLM
In today's fast-paced manufacturing environment, understanding the foundations of Computer-Aided Design (CAD), Computer-Aided Manufacturing (CAM), and Product Lifecycle Management (PLM) is crucial. This interconnectedness can lead to greater efficiency, innovation, and productivity. Each of these domains plays a significant role, influencing various stages of product development from conception through production and post-market management.
CAD is essential for designing product components and systems, allowing for detailed visual representations. It enables designers to create accurate models before any physical production begins. CAM takes these designs and realizes them, controlling machines to manufacture products with high efficiency. Finally, PLM helps manage the lifecycle of these products, ensuring that data is accessible and the operations are streamlined across teams.
The synergy between these three realms maximizes their individual strengths. Engineers using CAD can quickly conceptualize ideas and communicate visually. Manufacturers utilizing CAM can be more precise and reduce waste, and PLM provides oversight to guarantee that every aspect of the product lifecycle is managed effectively.
Moreover, this integration reduces the barriers between departments, fostering collaboration and improving overall organizational performance. It is not just about isolated technologies but rather their alignment that yields substantial competitive advantage and value.
"Understanding the interconnections between CAD, CAM, and PLM is vital for modern manufacturing success."
This section sets the stage for a deeper exploration into the definitions and functionalities of CAD, CAM, and PLM. By elucidating these concepts, we can appreciate how they interact and shape the future of product development.
Definition of CAD
Computer-Aided Design (CAD) refers to the use of software tools to create detailed 2D or 3D models that represent physical objects. CAD systems allow engineers and designers to visualize their ideas clearly and accurately. These tools provide functionalities such as drawing, modeling, and design simulations, facilitating a comprehensive understanding of how a product will perform.
CAD enhances design accuracy, reduces errors, and saves time, contributing significantly to the product development process. Designers can easily edit and revise models, making it a flexible solution for iterative design processes. Ultimately, CAD serves as the starting point for the production process, ensuring that every detail is considered before any manufacturing takes place.
Definition of CAM
Computer-Aided Manufacturing (CAM) is a technology that employs software to control machinery and equipment in the manufacturing process. By converting CAD drawings into a series of commands that machines can interpret, CAM streamlines the manufacturing workflow. It enhances precision, consistency, and efficiency in production.
CAM systems are capable of automating repetitive tasks, which reduces human error and increases throughput. They allow for the optimization of machining processes, leading to shorter production times and lower costs. This integration of software and machinery not only increases efficiency but also empowers manufacturers to respond quickly to market changes.
Definition of PLM
Product Lifecycle Management (PLM) encompasses the management of a product's lifecycle from inception through engineering and manufacturing to service and disposal. PLM systems act as a repository for all the data related to a product, allowing teams to access up-to-date information throughout its development and use.
Implementing PLM tools streamlines collaboration among different departments, ensuring everyone is working with the same data. It enables businesses to maintain compliance with regulations and standards. With PLM, organizations can analyze historical data for continuous improvements, ultimately enhancing product quality and reducing time to market.
In summary, CAD, CAM, and PLM are not just standalone systems; they form a critical triad that supports and optimizes the manufacturing process. As we delve deeper into their historical context and evolution, we will uncover how these technologies have shaped modern manufacturing practices.
Historical Context and Evolution
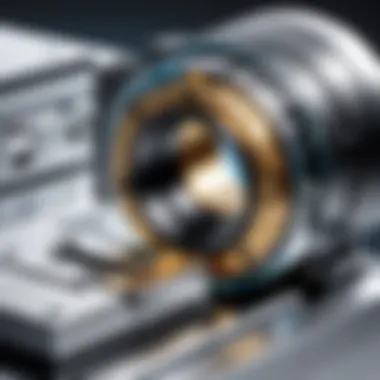
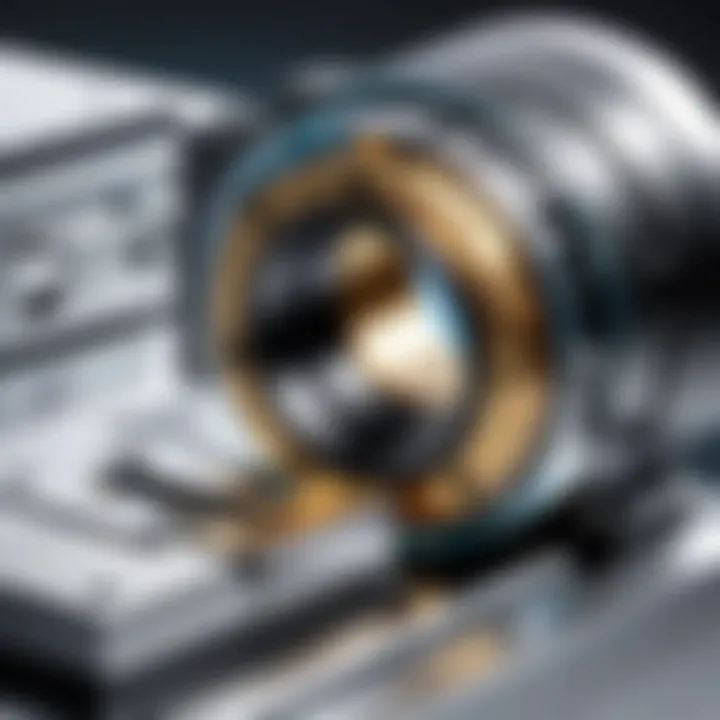
Understanding the historical context and evolution of Computer-Aided Design (CAD), Computer-Aided Manufacturing (CAM), and Product Lifecycle Management (PLM) is crucial for appreciating their present-day significance. These technologies evolved from separate disciplines into interconnected systems that enhance product design and manufacturing processes. By examining their origins, businesses can identify the advantages and challenges that have arisen over the years, informing future decisions regarding technology integration and utilization.
The Origin of CAD Technologies
CAD technologies began in the 1960s when industries sought ways to automate drafting processes. Initially, traditional manual methods were tedious and prone to errors. The introduction of instruments such as Sketchpad by Ivan Sutherland marked a revolutionary change. Sketchpad allowed users to manipulate graphical data on a screen for the first time. This innovation established the groundwork for modern CAD software.
As the years progressed, companies recognized the potential of using computers for engineering and design tasks. The 1970s and 1980s saw significant advances in CAD capabilities. 2D and later 3D modeling emerged, allowing designers to create sophisticated representations of their products. Companies like Autodesk and Dassault Systèmes played notable roles in developing industry-standard CAD solutions that frameworks today’s design processes.
Emergence of CAM in Manufacturing
CAM technology surfaced as a natural extension of CAD. As designs became more complex, manufacturers needed efficient ways to turn digital models into physical products. The integration of computers into various manufacturing processes led to the emergence of CAM in the 1970s.
CAM allows for the automation of manufacturing machinery through synchronization of design data and production machinery. This development led to increased precision, reducing waste and production time. Tools like CNC (Computer Numerical Control) machines exemplified this shift by allowing automated cutting and shaping of materials based on CAD outputs. The synergy between CAM and traditional manufacturing processes helped industries optimize production capabilities.
Development of PLM Systems
PLM systems came to light during the 1990s as businesses recognized the need for integrated management of product data throughout its lifecycle. Unlike CAD and CAM, which focused mainly on design and manufacturing, PLM encompasses a broader scope. It addresses not only product design and development, but collaboration amongst various teams and compliance with regulations.
PLM systems facilitate the entire process from conception through end-of-life of a product. This increased emphasis on data management ensures that all aspects of a product are recorded and easily accessible. Companies that adopted PLM systems benefited from improved coordination and better decision-making. Over time, PLM solutions have evolved to include cloud capabilities, enhancing collaboration across geographically dispersed teams.
"The evolution from CAD to CAM and finally to PLM showcases the necessity for integrated systems in modern manufacturing. Today, it is evident that these technologies do not operate in isolation."
Core Functionalities of CAD
Computer-Aided Design (CAD) is a pivotal component in various industries, especially in engineering, architecture, and product design. Its core functionalities play an essential role in enhancing design processes and streamlining workflows. Understanding these functionalities is vital for professionals aiming to leverage CAD tools optimally.
2D and 3D Modeling Capabilities
The ability to create both 2D and 3D models forms the backbone of CAD software. 2D design allows for precise representations of objects and layouts, making it ideal for technical drawings and schematics. Users can easily create lines, shapes, and dimensions that provide essential details for manufacturing processes.
In contrast, 3D modeling introduces depth and realism to designs. It allows users to visualize objects from multiple perspectives. The transition from 2D to 3D is significant because it enables designers to identify potential issues before production. This capability is crucial for validating geometry, aesthetics, and functionality. Industries such as automotive and aerospace benefit greatly from 3D modeling as they can simulate real-world performance and conduct various tests in virtual environments.
Collaboration Features
Collaboration is a key element in modern design activities. CAD software often includes features that promote teamwork, allowing multiple stakeholders to participate in the design process, regardless of their geographical location. These tools enable live sharing and simultaneous editing, where team members can contribute ideas and feedback in real time.
Moreover, CAD systems frequently incorporate version control and role-based access. This ensures that project teams work from the latest design revisions and helps prevent errors arising from outdated files. By facilitating effective communication among team members, CAD tools enhance creativity and foster innovation in design projects.
Integration with Other Software Tools
The integration of CAD with other software platforms is another core functionality that can significantly boost productivity. CAD designs often need to interface with tools for analysis, simulation, and manufacturing processes. For example, integration with Product Lifecycle Management (PLM) systems ensures that crucial product data is easily accessible across departments, enhancing collaboration and efficiency.
Software interoperability is vital for smooth workflow. Using programming interfaces, CAD tools can connect with Manufacturing Resource Planning (MRP) and Enterprise Resource Planning (ERP) systems, facilitating supply chain efficiency. This interconnectedness allows for the seamless transition of information throughout the product development lifecycle, ultimately saving time and reducing costs.
"CAD enables a holistic approach to design, combining creativity with precise technical specifications."
Key Advantages of CAM
Computer-Aided Manufacturing (CAM) offers several significant advantages that fundamentally enhance manufacturing processes. Understanding these advantages is crucial for businesses aiming to optimize production, lower costs, and improve overall efficiency. The key advantages of CAM are multifaceted, encompassing increased manufacturing efficiency, precision and accuracy, and strategic cost reduction.
Increased Manufacturing Efficiency
One of the foremost benefits of CAM is the noticeable increase in manufacturing efficiency. CAM systems streamline the production process by automating various tasks, such as toolpath generation and machine setup. This automation reduces the time required for manual interventions. Implementation of CAM allows for faster production cycles, which helps in meeting tight deadlines. Moreover, CAM software can optimize machining processes, ensuring that materials are utilized effectively.
Automation can lead to faster production cycles and improved throughput. Without such systems, manufacturers often face slower processes and increased downtime.
In essence, increased manufacturing efficiency via CAM contributes not just to time savings but also to enhanced adaptability. This means businesses can respond quickly to market changes or custom orders without sacrificing quality.
Precision and Accuracy
Precision and accuracy are critical in any manufacturing environment. CAM excels in this area by minimizing human error through automation. Advanced CAM systems utilize sophisticated algorithms to create highly accurate toolpaths. This ensures that each part produced conforms to the specified dimensions and tolerances.
Furthermore, CAM integrates well with CNC (Computer Numerical Control) machines, which enhances the repeatability of machining operations. Each manufactured item can achieve the same level of precision as the last, which is essential for industries such as aerospace and automotive, where tolerances are often extremely tight. The consistent output quality allows companies to maintain their reputation and meet regulatory standards efficiently.
Cost Reduction Strategies
Adopting CAM technologies also promotes cost reduction. By automating manufacturing processes, businesses can reduce labor costs since fewer operators are needed to oversee operations. In addition, CAM facilitates more efficient use of raw materials, minimizing waste through enhanced precision and optimized machining processes. This translates into lower material costs and fewer rework expenses.
CAM systems can also lead to reduced energy consumption due to better equipment utilization and lowered cycle times. Companies can analyze production data to identify areas for further efficiency improvements, leading to even greater cost savings over time.
In summary, the key advantages of CAM—enhanced manufacturing efficiency, heightened precision and accuracy, and strategic cost reduction—are vital for businesses looking to maintain a competitive edge in today's fast-paced market. Understanding these benefits enables organizations to leverage CAM technologies effectively, ultimately contributing to a more profitable and sustainable operational model.
The Role of PLM in Product Development
Product Lifecycle Management (PLM) plays a vital role in product development today. It serves as a backbone that supports the entire lifecycle of a product from ideation through to retirement. In this increasingly complex market, PLM not only streamlines processes but also enhances collaboration among teams, ensuring that a product meets market needs and regulatory standards efficiently.
Managing Product Data
Managing product data is at the core of PLM systems. Businesses generate vast amounts of data throughout a product's lifecycle. This can include specifications, design documents, and compliance requirements. A PLM system organizes this information systematically, allowing for easy access and retrieval. A centralized repository decreases the risk of data loss and inconsistency. It also enables version control, making it easier to track changes and updates over time.
When product data is well-managed, organizations can improve decision-making significantly. Having accurate and timely information means that teams work on the latest designs and requirements. Moreover, by leveraging PLM's capabilities, companies can even automate data collection processes, thus reducing manual entry errors and saving valuable time.

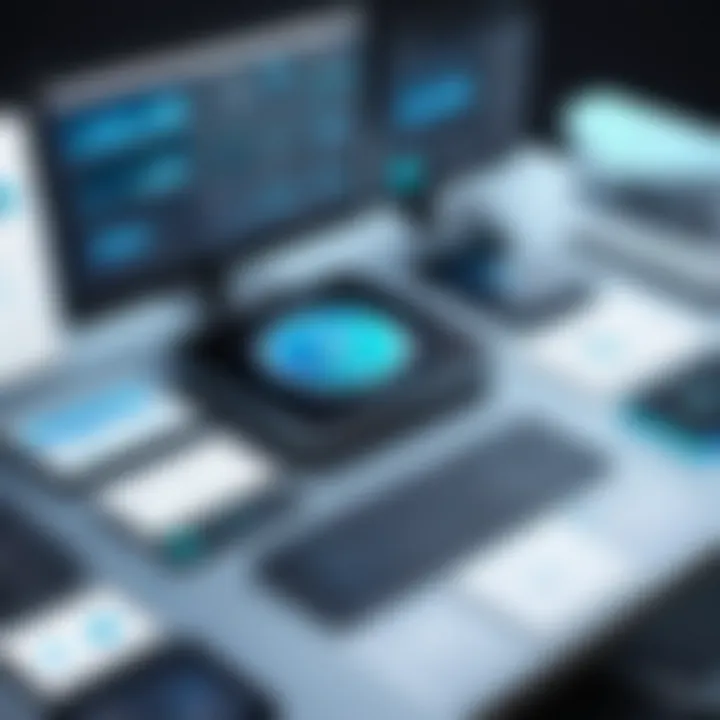
Synchronizing Team Efforts
Another crucial aspect of PLM is its ability to synchronize team efforts across various departments. In product development, collaboration between design, engineering, marketing, and manufacturing is essential. PLM provides tools that facilitate communication and integrate workflows, allowing teams to share insights and feedback seamlessly.
In a typical scenario, PLM software enables real-time sharing of documents and design files, reducing delays in project timelines. It also helps in assigning responsibilities and tracking progress, enhancing accountability. Effective synchronization can lead to shorter development cycles, ultimately bringing products to market faster.
"A well-integrated PLM system can significantly reduce time-to-market, giving organizations a competitive edge."
Facilitating Regulatory Compliance
Regulatory compliance is a critical factor in product development, especially in industries such as pharmaceuticals and aerospace. PLM helps ensure that all products adhere to relevant laws and standards. The software can automate compliance checks, keeping track of regulations that must be followed through every stage of the product lifecycle.
In addition, PLM systems store compliance documentation in an accessible manner. This ensures that whenever audits or inspections occur, necessary information is readily available. Failure to comply can lead to costly penalties or damage to a company's reputation. Therefore, leveraging PLM for compliance helps mitigate these risks systematically.
In summary, PLM plays an essential role in product development by managing product data, synchronizing team efforts, and facilitating regulatory compliance. Implementing a PLM strategy can lead to greater efficiency, reduced risks, and a higher quality end product.
Challenges Faced in CAD, CAM, and PLM Implementation
Implementing CAD, CAM, and PLM systems presents several challenges that organizations must navigate to fully leverage the advantages these technologies offer. Understanding these challenges is crucial for IT professionals, software professionals, and businesses aiming for effective integration and maximized efficiency. Poor implementation can lead to wasted resources, reduced productivity, and missed opportunities. Therefore, identifying these challenges can provide a pathway for organizations to overcome them and enhance their operational capabilities.
Resistance to Change
One significant hurdle is the resistance to change. Employees may feel threatened by new technologies, fearing job displacement or the need to learn new skills. This skepticism can lead to a lack of motivation in embracing CAD, CAM, or PLM systems. This resistance stems from several factors: lack of training, inadequate communication from management about the benefits, or simply the discomfort that comes with adapting to new processes.
To mitigate this, it is essential for leaders to foster an environment that encourages open communication and addresses the concerns of their teams. Providing comprehensive training programs and demonstrating the value of these systems can help ease the transition for employees.
Integration Issues
Integration issues present another major challenge in the implementation process. CAD, CAM, and PLM systems might be developed by different vendors and may not seamlessly communicate with one another. This lack of interoperability can cause data silos, which minimize the overall effectiveness of these systems.
Organizations often face difficulties in ensuring that data flows smoothly across platforms. These issues can arise from varying data standards, software compatibility problems, or simply the complexity of existing systems. To address these integration challenges, companies can invest in middleware solutions that act as intermediaries, facilitating smoother communication between disparate systems.
Cost Implications
Lastly, cost implications cannot be overlooked. Implementing CAD, CAM, and PLM technologies demands a substantial financial investment. From software licensing to employee training, the expenses can accumulate quickly. For some businesses, especially smaller ones, these costs can pose a significant barrier.
However, failing to invest in these systems can lead to greater losses in terms of inefficiency and outdated processes. It is important for businesses to look at the long-term savings these technologies can provide. By improving workflow and reducing errors, the initial costs can often be recouped over time.
Investing wisely in CAD, CAM, and PLM systems can transform the operational landscape, leading to sustainable growth and improved efficiency.
In summary, addressing resistance to change, resolving integration issues, and thoughtfully considering cost implications are critical factors in the successful implementation of CAD, CAM, and PLM systems. Through careful planning and proactive management, organizations can overcome these challenges and reap the rewards of integrated technology.
Integration of CAD, CAM, and PLM
The integration of Computer-Aided Design (CAD), Computer-Aided Manufacturing (CAM), and Product Lifecycle Management (PLM) is pivotal for modern manufacturing and product development frameworks. Each system contributes uniquely to the development process, and their overlapping functionalities create a synergy that enhances productivity and innovation. As organizations strive for operational excellence, the cohesive melding of these systems becomes essential to streamline workflows and optimize the entire product lifecycle.
One of the primary advantages of such integration is the facilitation of data flow across different stages of the production process. In a traditional setup, the lack of integration often leads to silos of information, which can hinder accurate decision-making. By integrating CAD, CAM, and PLM systems, companies can achieve real-time data visibility. This transparency ensures that all stakeholders, from design engineers to manufacturing professionals, have access to the same updated data. Therefore, reducing discrepancies and minimizing errors.
Benefits of Integration
The benefits of integrating CAD, CAM, and PLM are numerous. They include:
- Improved Collaboration: Teams can work on unified platforms, sharing insights and amendments instantly, which decreases the time to market.
- Enhanced Efficiency: Automated processes reduce the need for manual data entry, freeing up valuable time and resources.
- Cost Savings: By optimizing workflows and minimizing rework, businesses can significantly cut operational costs.
- Quality Control: Integrated systems allow for consistent monitoring and adjustments, leading to higher product quality and compliance with industry standards.
- Faster Innovation: The holistic view provided by integrated systems fosters an environment conducive to innovation, allowing companies to react swiftly to market changes.
"The integration of CAD, CAM, and PLM is not just about technology; it is about unifying the ecosystem in which products are designed, manufactured, and managed throughout their lifecycle."
Strategies for Effective Integration
To maximize the advantages of integrating CAD, CAM, and PLM systems, organizations must employ strategic approaches:
- Assessment of Current Systems: Evaluate existing tools to identify gaps and compatibility issues. This will help in selecting the right systems for integration.
- Define Clear Objectives: Establish specific goals such as improving efficiency or reducing costs to guide the integration process.
- Choose Compatible Software: Selecting software that supports interoperability can ease integration challenges. For instance, software like SolidWorks for CAD can be effectively integrated with manufacturing execution systems (MES).
- Training and Change Management: Educate employees about the new integrated systems to ensure smooth transitions. Addressing resistance to change is crucial for adoption.
- Continuous Monitoring and Improvement: After integration, ongoing assessments and updates are vital. This helps in keeping systems relevant and effective as technologies evolve.
Future Trends in CAD, CAM, and PLM
The rapid evolution of technology mandates a continuous review of the functionalities associated with CAD, CAM, and PLM systems. These systems are at the heart of modern manufacturing and product development. Understanding future trends is essential not only for staying competitive but also for embracing innovative methodologies. Various elements like AI advancements, cloud computing, and more collaborative tools are emerging and changing the landscape.
Benefits associated with these trends can significantly enhance productivity, precision, and flexibility within organizations. Adapting to these innovations can mitigate risks and ensure that businesses remain relevant in an ever-changing market. Consideration about how these systems integrate can lead to transformative efficiency and innovation.
"To stay ahead in the tech landscape, emerging technologies in CAD, CAM, and PLM must be recognized and utilized effectively."
Advancements in AI and Machine Learning
AI and machine learning are transforming how CAD, CAM, and PLM systems function. They enable predictive analytics, which helps organizations anticipate project requirements. For example, AI can analyze previous designs to suggest improvements or detect potential errors in new models. This leads to a reduction in time spent on revisions.
In manufacturing, machine learning optimizes the production process by examining data from various stages. It can identify patterns that help in quality assurance, reducing the likelihood of defects early in the production cycle. Moreover, these advancements facilitate smarter resource allocation by predicting needs for materials and machinery.
Some features worth noting include:
- Automated Design Adjustments: CAD systems can now suggest modifications automatically based on performance metrics.
- Real-Time Data Processing: AI enables instant feedback during the design to manufacturing transition.
- Enhanced User Interfaces: Machine learning creates adaptive user experiences, tailored for individual user behavior.
The Role of Cloud Technology

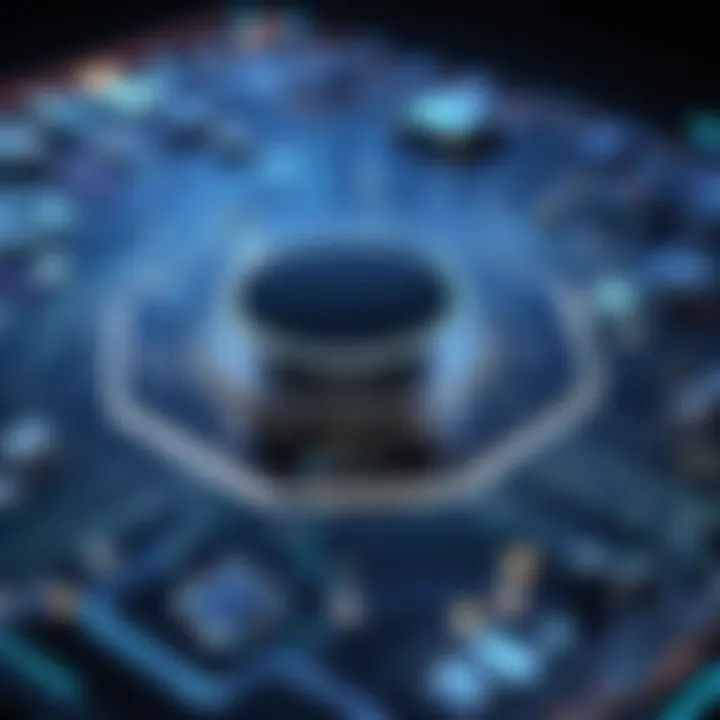
Cloud technology is becoming a critical component in the integration of CAD, CAM, and PLM systems. It provides a centralized platform that allows for better collaboration and accessibility. Multiple teams across different locations can access data and work simultaneously on projects without delays.
Key aspects of cloud technology in these realms include:
- Scalability: Organizations can adjust their resources based on current needs without significant upfront investments.
- Data Security: Cloud providers often offer advanced security measures, ensuring that critical information is protected from unauthorized access.
- Cost Efficiency: The shift to cloud reduces the need for physical infrastructure and lowers maintenance costs.
Moreover, as businesses move more functions to the cloud, integration between CAD, CAM, and PLM becomes smoother. Data can be shared instantly, ensuring that all aspects of product development are synchronized. Cloud solutions also facilitate real-time updates and communication, essential for agile project management.
Comparative Analysis of Leading Software Solutions
A comparative analysis of leading software solutions is essential in understanding how various tools in CAD, CAM, and PLM ecosystems contribute to streamlined workflows and enhanced productivity. This analysis helps professionals choose the right software that aligns with their operational needs and objectives. It brings clarity to the functionalities, strengths, and weaknesses of different options available in the market.
Understanding specific software offerings allows organizations to identify gaps in their processes and make informed decisions. Each software package has unique features that cater to distinct aspects of design, manufacturing, and product management. Therefore, making a well-informed choice can significantly impact efficiency and ultimately the bottom line.
The importance of conducting such analyses extends to risk management, as they help mitigate the uncertainties associated with deployment and integration. By knowing what each tool offers, teams can anticipate challenges and capitalize on opportunities presented by these technologies.
CAD Software Options
When discussing CAD software, several reputable options present themselves. Software like AutoCAD has long held a significant place in the industry due to its robust 2D and 3D modeling capabilities. SolidWorks offers a user-friendly interface and excels in parametric design, making it a favorite in mechanical engineering. Another solution, CATIA, stands out for its ability to handle complex assemblies, especially in industries like aerospace and automotive.
The choice of CAD software should consider the following factors:
- Functionality: Assess if the software meets specific design requirements.
- Integration capabilities: Check how well it works with CAM and PLM systems.
- User experience: A robust interface can enhance productivity.
- Cost efficiency: Evaluate the pricing model against provided features.
By analyzing these software options, organizations can determine which CAD solution aligns with their operational goals.
Top CAM Tools
In the realm of CAM, several tools stand out for their efficiency and effectiveness in converting designs into usable manufacturing instructions. Mastercam is one of the leading tools, known for its extensive machining capabilities. Fusion 360, another notable option, combines CAD and CAM systems, offering streamlined processes for users.
Key considerations when selecting CAM tools include:
- Machining capabilities: Verify if the software supports desired machining processes.
- Material compatibility: Ensure the tool can handle the materials used in production.
- Simulation options: Assess how well the tool can model the machining process.
- Ease of use: Consider the learning curve associated with various CAM tools.
These factors play a crucial role as they directly impact the production process.
PLM Platform Comparisons
PLM platforms serve as the backbone for product lifecycle management, enabling organizations to manage their products through each stage efficiently. Siemens Teamcenter is among the leaders, providing comprehensive solutions for data management and collaboration. PTC Windchill offers features that prioritize change management and regulatory compliance.
When comparing PLM platforms, consider the following:
- Scalability: Ensure the software can grow with the organization.
- Data handling capabilities: Check how the platform manages complex product data.
- Collaboration features: Look for tools that enhance teamwork across departments.
- Integration: Evaluate how well the PLM software works with CAD and CAM tools.
Considering these elements helps enterprises choose the right PLM software for their needs. As companies grow and product lines expand, the right PLM system becomes essential for staying organized and compliant.
Real-World Applications of CAD, CAM, and PLM
The interplay of Computer-Aided Design (CAD), Computer-Aided Manufacturing (CAM), and Product Lifecycle Management (PLM) significantly influences numerous industries. This section analyzes their real-world applications, showcasing how they enhance efficiency, innovation, and collaboration in diverse sectors. Each application reveals unique insights into the advantages these technologies bring and the crucial considerations for their implementation.
Case Studies in Aerospace
The aerospace industry is a prime example of how CAD, CAM, and PLM create synergies that enhance product development and manufacturing complexity. Companies like Boeing employ CAD for the initial design of aircraft components, allowing for intricate modeling of assemblies that adhere to strict regulations. With CAM, those designs convert into tangible products through automated machinery, ensuring high precision in component fabrication.
Moreover, PLM systems at firms like Airbus manage data across different teams, allowing for a synchronized approach to development and compliance. These platforms track changes in real-time, providing visibility into every phase of the product's lifecycle. The result is reduced lead times and improved collaboration that meets stringent safety regulations. This integration not only optimizes production schedules but enhances quality assurance processes as well, which is crucial in aerospace where safety is paramount.
Manufacturing Sector Innovations
In the manufacturing sector, the synergy of CAD, CAM, and PLM is driving innovations that redefine traditional production processes. Companies that implement this integrated approach can significantly shorten the time from design to production. For instance, General Motors uses CAD for designing vehicle parts and utilizes CAM for efficient machining processes. This alignment reduces errors and streamlines workflow.
With PLM, manufacturers can manage vast amounts of data concerning product development and regulatory compliance, facilitating better decision-making. As a result, they can adapt quickly to market demands, optimize resource allocation, and improve product quality. Ultimately, these practices yield lower production costs and bolster competitive advantage in a dynamic market.
Product Development Best Practices
Adopting a cohesive strategy for CAD, CAM, and PLM is essential for best practices in product development. Companies should focus on several key areas to fully leverage these technologies:
- Cross-Functional Teams: Encourage collaboration among design, engineering, and manufacturing teams from the outset. This collaboration allows for seamless transitions between stages and mitigates potential issues related to misunderstanding specifications.
- Iterative Prototyping: Utilize rapid prototypes created through CAD, validated through CAM processes. This method permits early detection of design flaws and fosters an environment of continual improvement.
- Data Management: Invest in robust PLM architectures that maintain traceability of all modifications throughout the product's lifecycle. Proper data management enhances decision-making and compliance with industry standards.
The End
The conclusion of this article emphasizes the significant interconnections among CAD, CAM, and PLM in modern product development and manufacturing processes. Understanding these relationships is crucial for professionals aiming to leverage technology for enhanced efficiency and innovation. Each component—CAD for design, CAM for manufacturing, and PLM for lifecycle management—serves a unique purpose but together they create an integrated system that maximizes productivity and reduces errors.
Recap of Key Insights
Each section discussed the fundamental aspects of CAD, CAM, and PLM. Key insights include:
- CAD enhances design accuracy and facilitates collaboration among teams, which is essential in today’s complex projects.
- CAM improves manufacturing efficiency through automation, ensuring precision in the production processes.
- PLM plays a vital role in managing products throughout their lifecycle, enabling synchronization across teams and ensuring compliance with regulations.
Additionally, the article highlighted how the integration of these systems can lead to substantial benefits such as:
- Streamlined Processes: Integrated systems reduce redundancies and lead to quicker project completions.
- Cost Efficiency: Through better management and reduced errors, organizations can see significant cost savings.
- Improved Collaboration: Teams can work together in real-time, enhancing communication and reducing misunderstandings.
"The future of product development lies in the seamless integration of design, manufacturing, and lifecycle management."
The Path Forward
Looking ahead, the integration of CAD, CAM, and PLM is increasingly important. As industries evolve and become more complex, these systems will need to adapt to new technologies, such as artificial intelligence and machine learning. Embracing technological advancements will help organizations to stay competitive.
Companies should consider adopting cloud technology to enable access and control across multiple locations, promoting collaboration and responsiveness to market changes. Training and development for employees on new tools will also be essential for successful integration.