Harnessing CAD Software for Modern Manufacturing
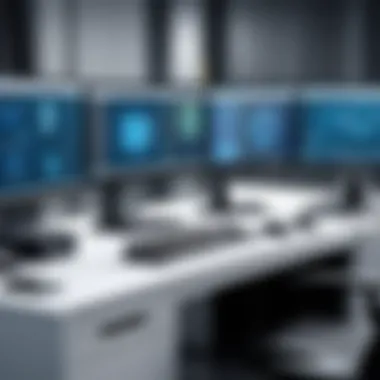

Intro
In recent years, the advancement of technology has reshaped numerous industries, and manufacturing is no exception. Within this context, Computer-Aided Design (CAD) software has emerged as a fundamental tool. Its influence extends beyond mere drafting and design; it plays a crucial role in enhancing efficiency, accuracy, and teamwork across various stages of production. As small and large businesses alike adopt this technology, understanding CAD's integration becomes increasingly relevant.
This article delves into various aspects of CAD software utilized in manufacturing environments. From core functionalities to user insights, we will explore how these tools optimize workflows. The dialogue also encompasses the implications of adopting such technology in modern factories, setting a framework for informed decision-making.
Software Overview
Software Features
CAD software comes equipped with a myriad of features that cater to the diverse needs of the manufacturing sector. Key functionalities include:
- 3D Modeling: Allows designers to create detailed three-dimensional representations of products.
- Simulation and Analysis: Enables testing of designs under various conditions to predict performance and identify potential weaknesses.
- Collaboration Tools: Facilitates real-time sharing and editing of designs among team members, essential for coherence in large projects.
- Documentation: Automates the generation of necessary documentation, such as blueprints and materials lists, reducing manual effort.
Technical Specifications
The effectiveness of CAD software is also tied to its technical specifications. A robust system typically includes:
- Processing Power: High-performance CPUs and GPUs to handle complex calculations and graphic rendering.
- Memory Requirements: Ample RAM to support multitasking and large file processing.
- File Compatibility: Support for various file formats to ensure seamless integration with other systems.
Peer Insights
User Experiences
Understanding CAD software from the end-user perspective can offer valuable insights. Many users report enhanced productivity and reduced errors in their design processes. This is particularly evident in workflows where multiple stakeholders are involved. Users also appreciate the vast online libraries of templates and designs that facilitate quicker project initiation.
Pros and Cons
While the advantages of CAD software are prominent, there are also some potential drawbacks. Here are key points:
Pros:
- Increased design accuracy.
- Improved signaling among teams, which leads to quicker decision-making.
- Difficulty in training new users, as advanced features might require significant learning.
Cons:
- Initial setup costs can be prohibitive for smaller enterprises.
- Software updates may require ongoing investments and adaptations in training.
"Investing in CAD software is not just about design; it’s an investment in overall productivity and efficiency."
In summary, while CAD software brings substantial benefits, the varied experiences and considerations indicate that its integration needs careful planning. This article will deepen the analysis in further sections to equip professionals with the information necessary to navigate the complexities of modern manufacturing software.
Prologue to Factory CAD Software
The landscape of manufacturing has evolved significantly over the past few decades. One of the key technologies influencing this change is Computer-Aided Design (CAD) software. This section will explore the role of CAD software in modern factory settings, its relevance in production efficiency, and the advantages it brings to design processes.
CAD software is not just a tool; it is a fundamental component in the manufacturing ecosystem. In factories, it enables designers and engineers to create precise models, simulate processes, and communicate seamlessly with stakeholders. Its integration allows for faster adjustments and iterations, reducing the time from concept to production. This agility is crucial, as market demands shift rapidly, requiring manufacturers to be both adaptable and efficient in their operations.
Definition of CAD Software
Computer-Aided Design software refers to programs that facilitate the creation, modification, analysis, or optimization of a design. Using CAD software, individuals can create 2D drawings or 3D models that represent real or conceptual constructs. These tools can encompass various functionalities, such as dimensioning, editing, and rendering.
Different forms of CAD software cater to specific needs in manufacturing:
- 2D CAD Software enables engineers to draft and detail drawings without necessarily moving to a three-dimensional space.
- 3D CAD Software allows for more dynamic visualization and modeling of products.
- Parametric CAD Software adjusts models based on defined parameters, making it easy to alter designs.
Understanding CAD's nature and capabilities is vital for integrating it into manufacturing workflows.
Historical Context
The origins of CAD software trace back to the 1960s. Initial developments were primitive, focused primarily on creating basic geometrical shapes and designs. Over time, as computing technology improved, CAD software became more advanced, leading to the capability to create complex 3D models and simulations.
In the 1980s, CAD software began garnering widespread adoption among manufacturers. As personal computers became more accessible, professionals started integrating CAD into their processes. Industrial giants like AutoCAD and SolidWorks emerged as leaders, offering increasingly sophisticated tools for design and modeling.
Today, CAD software is ubiquitous in manufacturing, overwhelmingly replacing traditional drafting methods. It provides mechanisms for collaboration that were unimaginable just a few decades ago. This historical perspective highlights how CAD software transitioned from niche applications to essential tools in any manufacturing toolkit, shaping how products are designed and fabricated in factory settings.
Key Features of Factory CAD Software
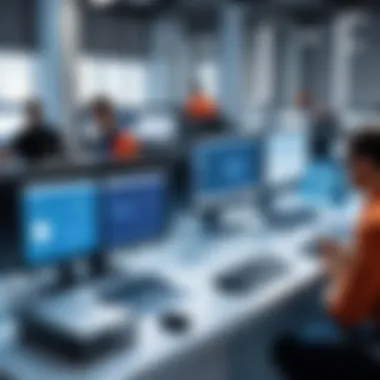

The landscape of modern manufacturing is evolving quickly. Central to this change is the integration of Computer-Aided Design (CAD) software. This software offers various features that can significantly improve production operations. Understanding these features is essential for organizations looking to enhance their design processes, streamline workflows, and minimize errors.
3D Modeling Capabilities
One of the standout features of factory CAD software is its 3D modeling capabilities. This allows designers to create precise three-dimensional representations of products. Unlike traditional drafting methods, 3D modeling provides a more accurate view of the final product. This feature helps identify potential design flaws early in the process. It also enables better visualization, aiding in design reviews and presentations.
The ability to manipulate models in a three-dimensional space grants designers greater freedom. Changes can be made quickly, facilitating iterative design processes. These capabilities are especially beneficial for complex assemblies where precision is critical. Furthermore, 3D models can be used directly in simulation tools, helping manufacturers analyze functionality before physical production.
Simulation and Analysis Tools
Simulation and analysis tools present another crucial aspect of factory CAD software. These tools enable manufacturers to test a product’s performance in a virtual environment. Different conditions can be simulated to see how a design reacts under stress, temperature changes, or movement. This is particularly important in sectors like automotive and aerospace, where safety and reliability are paramount.
Such testing reduces the need for costly physical prototypes. It allows teams to make informed decisions based on data rather than assumptions. By integrating simulations early in the design process, companies can also reduce the time-to-market for new products. This results in significant overall cost savings.
"The integration of simulation tools results in a design process that is not only faster but also more reliable."
Collaboration and Communication Features
As organizations become more interconnected, the need for effective collaboration and communication features in CAD software grows. Modern CAD systems allow multiple users to work on a design simultaneously. This capability fosters teamwork, particularly in large projects involving cross-departmental efforts.
Moreover, cloud-based CAD solutions enhance this collaboration further. Teams can access designs from anywhere, enabling remote work. This flexibility is crucial in today’s global marketplace. The software also typically provides version control features, ensuring all team members are looking at the most current design. Such capabilities minimize confusion and reduce errors that could arise from working on outdated files.
The Importance of CAD Software in Manufacturing
Computer-Aided Design (CAD) software plays a vital role in modern manufacturing. It is more than just a tool for drawing and modeling; it is a critical component that enhances overall operational efficiencies. As industries evolve, the necessity for precise designs, effective production processes, and reduced costs has fueled the adoption of CAD software across various sectors. Its significance rests in several aspects that provide a clear advantage over traditional manufacturing methods.
Enhancing Design Precision
One of the primary benefits of CAD software is its capability to enhance design precision. Traditional drafting methods are often prone to errors due to human factors. In contrast, CAD software utilizes advanced algorithms and automated features that minimize mistakes. Designers can create intricate and detailed models with high accuracy, leading to fewer revisions and better product quality.
Moreover, CAD software allows for real-time adjustments to designs. This adaptability is crucial when product specifications change or when venturing into new markets. The ability to visualize projects in 3D also aids in identifying design flaws before production begins. This proactive approach significantly reduces the likelihood of costly errors during manufacturing, contributing to the overall success of projects.
Streamlining Production Processes
CAD software also plays an indispensable role in streamlining production processes. It facilitates a seamless transition from design to manufacturing. The integration of CAD with Computer Numerical Control (CNC) systems means that designs can be directly converted into machine instructions with minimal human intervention.
This streamlining leads to faster turnarounds on production schedules. When production teams have access to precise design files, they can manufacture products more efficiently. Additionally, CAD software allows teams to simulate manufacturing processes before actual implementation. This foresight enables better planning and resource allocation, which are critical for maintaining workflow efficiency.
Cost Reduction and Efficiency
Finally, utilizing CAD software can lead to significant cost reductions. In an age where every dollar counts, minimizing waste and maximizing resource utilization is essential. CAD software aids in optimizing material use by allowing for precise calculations of quantities needed for each project. This capability leads to less waste and lower material costs.
Furthermore, the efficiency gained through improved design precision and streamlined production processes translates into overall operational cost savings. Organizations that implement CAD solutions often see reductions in labor costs as well. As fewer revisions are required and production runs more smoothly, staff can focus on value-added tasks rather than fixing errors or delays.
Efficiency is no longer a luxury, but a necessity for survival in the competitive manufacturing landscape.
Different Types of Factory CAD Software
Understanding the different types of Factory CAD software is crucial for organizations looking to enhance their design processes. Each type of CAD software offers unique features and functionalities, which fulfill diverse design requirements within manufacturing environments. Selecting the appropriate type can lead to significant improvements in workflow efficiency, product quality, and overall productivity. In the sections that follow, we delve into the three main categories of Factory CAD software: Parametric CAD, Direct Modeling CAD, and Sheet Metal Design Software. We will discuss their individual benefits, use cases, and considerations for implementation.
Parametric CAD Software
Parametric CAD software is designed around a core concept: parameters. This type of software allows users to create 3D models based on defined parameters that govern the geometry and relationships of the design elements. One of the key advantages is the ability to make quick changes to dimensions or features, automatically updating the entire model without the need to redefine every detail.
Benefits:
- Flexibility: Designers can easily modify designs in response to changes in requirements or conditions, making it highly adaptable for evolving projects.
- Consistency: Since all dimensions and constraints are interconnected, maintaining design standards is simplified.
Considerations:
Implementing parametric CAD software may require training personnel to effectively utilize its powerful features. Organizations must also consider their specific needs, as not every project may benefit from the level of complexity this software provides.
Direct Modeling CAD Software
Direct modeling CAD software stands out for its user-friendly approach. It allows designers to manipulate geometry without the need for parameters or history trees. This can be especially advantageous for those who need to produce quick modifications or conduct rapid prototyping.
Benefits:
- Speed: Designers can make changes on-the-fly, enhancing the speed of the design process.
- Intuitive Interface: Most direct modeling tools come with a more straightforward interface that appeals to less experienced users.
Considerations:
While direct modeling is efficient, it may lack some capabilities found in parametric CAD software. Organizations should evaluate the depth of modeling required for their projects, as it could affect long-term productivity if complex designs are frequently needed.
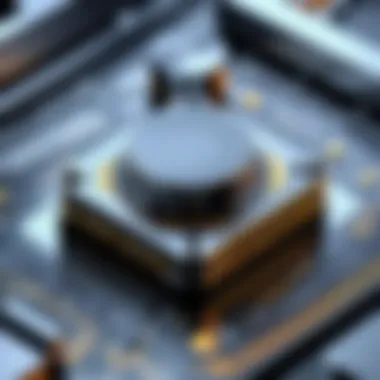

Sheet Metal Design Software
Sheet metal design software specializes in the unique requirements of sheet metal fabrication. It incorporates specific tools and functionalities to streamline the design process of flat metal components, ensuring that designs can be easily converted into viable product manufacturing.
Benefits:
- Tailored Features: This type of software typically includes tools for folding, tabbing, and bending, thus eliminating the guesswork in the fabrication process.
- Optimization for Fabrication: Users can create designs that minimize waste through efficient material usage and fabrication techniques.
Considerations:
Although effective for its intended use, sheet metal design software may not be suitable for all manufacturing needs. Companies must assess whether their operations are heavily focused on sheet metal or if additional CAD capabilities are necessary.
"Choosing the correct CAD software type influences not only the design quality but also the organization’s workflow efficiency."
In summary, the type of Factory CAD software selected will greatly impact how design processes are carried out in manufacturing settings. By taking into consideration the unique characteristics of each type, companies can make informed choices that align with their specific product development strategies.
Implementation Strategies for Factory CAD Software
Effective implementation strategies are crucial when integrating factory CAD software. These strategies define how technology will transform manufacturing processes. When deploying a CAD system, there are several key elements to consider. The decision-making process must align with organizational objectives and the specific needs of the workforce.
Assessing Organizational Needs
To begin the integration process, it is essential to accurately assess organizational needs. This step involves understanding current workflows, bottlenecks, and inefficiencies. Engaging with employees across different departments provides valuable insights. Employees can share their challenges and preferences regarding design and production processes. It’s important to focus on areas where CAD software can deliver the most impact.
One way to gather this information is through surveys or structured interviews. Asking precise questions about existing tools and processes can reveal gaps that a new CAD solution can fill. Additionally, observing current processes directly can provide an objective view of operational inefficiencies. With a comprehensive understanding of the organization’s unique requirements, businesses can select CAD tools that effectively address those needs.
Training and Skill Development
Once the organizational needs are assessed, the next crucial step is training and skill development. CAD software typically offers advanced features, which can be complex for new users. Therefore, tailored training programs are essential. Companies should consider leveraging various methods for training employees, such as hands-on workshops, online courses, and mentorship.
A key aspect is to identify employees who will become champions of the CAD software within their teams. This strategy creates a support network for users who are less familiar with the software. Continuous learning should be encouraged, as software updates can introduce new functionalities and tools. Regular training sessions not only enhance skill sets but also foster a culture of innovation.
Integration with Existing Systems
Another significant strategy is seamless integration with existing systems. Most organizations use a range of software for different functions, such as Enterprise Resource Planning (ERP) systems, Customer Relationship Management (CRM) software, and other applications. Effective CAD integration involves ensuring that these systems can communicate fluidly.
This integration allows for smoother data exchange and ensures that design changes are reflected throughout the organization. It is vital to involve IT teams early in the adoption process. They can provide insights into potential integration challenges and solutions. Successful integration can lead to enhanced productivity and reduced manual data entry, which can significantly decrease errors.
"A well-thought-out implementation strategy is crucial for maximizing the benefits of CAD software."
By assessing organizational needs, investing in employee training, and ensuring compatibility with existing systems, companies can facilitate a smooth transition. These steps ultimately lead to enhanced efficiency, improved design precision, and greater collaboration across teams.
Evaluating CAD Software Solutions
Evaluating CAD software solutions is a critical step for companies looking to enhance their manufacturing processes. With a wide array of options available, making an informed choice can significantly impact productivity and efficiency. The right software can streamline workflows, reduce errors, and ultimately lead to a better end product. Therefore, businesses must carefully assess their needs, considering various elements such as features, user experience, and support.
Comparison of Features
When comparing CAD software solutions, features are paramount. Each program offers different capabilities that cater to diverse industries. Here are some essential features to consider:
- 3D Modeling: Essential for visualizing designs in a realistic manner.
- Simulation Tools: Help in testing designs before production, which can save time and reduce costs.
- File Compatibility: Ensure the software works well with other tools and formats used within the industry.
- Scalability: Important for growing businesses that may need additional features or capacity in the future.
- Customization Options: A competitive edge is often gained through tailored features that meet specific business requirements.
By analyzing these features, businesses can identify which CAD software aligns best with their objectives.
User Experience and Support
User experience plays a significant role in the effective utilization of CAD software. A well-designed interface can make a considerable difference in how efficiently users navigate the software. Key considerations include:
- Ease of Use: Software should be intuitive and user-friendly, minimizing the learning curve for new users.
- Technical Support: Reliable customer service is crucial, especially when facing technical challenges. Access to support resources, like tutorials and community forums, enhances the overall user experience.
- Training Resources: Some software providers offer extensive training programs, which can be beneficial for onboarding staff and maximizing productivity.
In summary, evaluating CAD software solutions requires attention to detail. By comparing specific features and considering user experience and support, businesses can make decisions that will enhance their manufacturing capabilities, ensuring that they invest in software that meets their needs effectively.
Future Trends in Factory CAD Software
The future of Factory CAD software is reshaped by technological innovations and evolving industry needs. Understanding these trends is vital for companies aiming to stay competitive in the manufacturing landscape. As industries embrace digital transformation, CAD software continues to adapt to incorporate advanced technologies, enhancing functionalities and user experience.
Integration with AI and Machine Learning
The integration of Artificial Intelligence (AI) and Machine Learning (ML) into CAD software marks a significant shift in design processes. These technologies allow computers to analyze vast sets of data and improve design accuracy based on previous outcomes. AI assists in predictive modeling, helping manufacturing entities anticipate defects or issues during the design phase. This leads to reduced modifications during production, saving both time and costs.
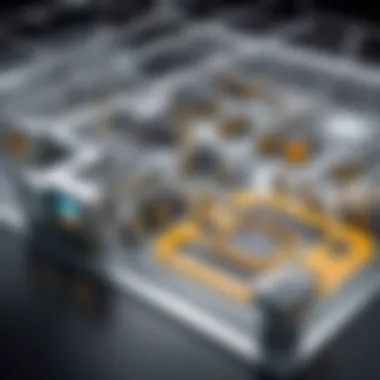

Using AI tools, engineers can automate repetitive tasks that often consume time. This automation improves productivity, freeing designers to focus on innovative outcomes. Moreover, Machine Learning algorithms can learn from previous design projects, suggesting intelligent modifications or enhancements, thus fostering an adaptive design environment. By implementing AI and ML, businesses can improve overall efficiency, reduce error rates, and significantly shorten product development cycles.
Cloud-Based CAD Solutions
Cloud-based CAD solutions have emerged in response to the growing demand for flexibility and collaboration. By hosting CAD software on the cloud, companies gain access to designs from anywhere, facilitating remote work and enhancing team collaboration. This approach simplifies sharing drawings and designs across departments and locations, encouraging real-time feedback and modifications.
Security is another strong point for cloud-based solutions. Data stored on the cloud is often more secure than traditional local storage. Most providers implement state-of-the-art protection measures, reducing the risk of data loss or breaches. Furthermore, cloud solutions offer scalability, meaning companies can adjust their software usage according to project demands without significant upfront investments in hardware. This scalability also includes handling peak workloads and integrating additional tools as needed.
Adopting cloud-based CAD software allows organizations to keep up with rapid technological changes without enduring heavy costs associated with traditional installations. Companies can integrate the latest updates instantly without the need for extensive upgrades or downtime.
Case Studies of Successful CAD Implementation
The integration of CAD software in manufacturing cannot be fully appreciated without examining real-life examples. These case studies highlight the practical benefits and challenges that industries face. They serve as a guide for other businesses considering similar implementations. Understanding these successes informs best practices and inspires confident decision-making.
Automotive Industry
The automotive sector stands as a prominent example of CAD software integration. Major manufacturers like Ford Motor Company and General Motors employ advanced CAD solutions to streamline their design processes. With CAD, these companies develop intricate vehicle designs while ensuring compliance with safety and regulatory standards.
- Design Efficiency: CAD tools enable automotive engineers to create complex 3D models rapidly. For instance, Ford uses systems such as CATIA to enhance design workflows. These programs facilitate a better visualization of parts and assembly, leading to quicker approvals.
- Problem Solving: Using software simulations, engineers can conduct stress analysis and weight distribution checks. Volkswagen’s use of CAD allowed them to resolve design issues early in the development phase, thus reducing costly revisions later.
- Collaboration Across Departments: CAD software encourages collaboration among different teams. Designers, engineers, and manufacturers can share updates in real time, enhancing communication. Honda has adopted an integrated approach where all teams access the same models, reducing delays.
In summary, the automotive industry benefits significantly from CAD integration. The results include lowered costs, enhanced design processes, and improved team collaboration.
Aerospace Sector
In the aerospace industry, CAD software's role is indispensable. Companies like Boeing and Airbus rely on sophisticated CAD systems to produce reliable and safe aircraft. The intricacies involved in aerospace design necessitate a detailed and precise approach that CAD software provides.
- Precision in Design: Precision is non-negotiable in aerospace design. CAD tools, such as Siemens NX, allow engineers to create highly detailed designs vital for aerodynamics and safety. The ability to simulate airflow and stress ensures that designs meet the exacting standards of the industry.
- Cost Management: The implementation of CAD solutions in aerospace aids in tracking costs effectively. Projects like the Boeing 787 Dreamliner leveraged CAD to manage expenditures associated with thousands of components across various suppliers. This capability reduces wastage and enhances budgeting.
- Regulatory Compliance: The aerospace sector faces stringent regulations. CAD systems help firms trace compliance with necessary guidelines through detailed documentation and design records, making audits manageable. Airbus has utilized CAD for ensuring its designs meet FAA regulations without excessive resource costs.
To summarize, the aerospace sector’s success with CAD software stems from improved design precision, effective cost management, and seamless compliance with various regulations. These case studies not only demonstrate great returns on investment but also underscore the strategic value of integrated design technologies.
Challenges and Limitations of Using CAD Software
The integration of CAD software into modern manufacturing brings numerous advantages. However, it also surfaces challenges and limitations that cannot be overlooked. These aspects are crucial for organizations to consider when embarking on the adoption of CAD technologies. Understanding these challenges helps companies prepare effectively, enabling a smoother transition to a more efficient design and manufacturing environment.
High Initial Investment Costs
One of the most significant barriers to implementing factory CAD software is the high initial investment costs. The software itself can be quite expensive, with licenses for advanced systems like SolidWorks, AutoCAD, or CATIA often costing thousands of dollars. This cost does not include necessary hardware upgrades or additional peripheral devices required for optimal performance. Companies must also develop a budget for ongoing maintenance and updates, which can add to financial strain.
These upfront costs can be prohibitive for small and medium-sized businesses. It may lead them to delay or avoid adopting CAD solutions altogether. They often consider outsourcing to third-party providers, which can become costly over time. Thus, while CAD software offers many long-term benefits, the initial financial commitment demands careful evaluation and planning.
Requirement for Continuous Training
The need for continuous training presents another challenge. As technology evolves rapidly, factory CAD software also undergoes frequent updates and iterations. Without ongoing training, employees may not fully benefit from new features or improvements. This situation can lead to underutilization of the software and missed opportunities for productivity gains.
Training programs can be resource-intensive. They often require time away from regular work duties, which may affect production schedules. Additionally, companies must budget for training costs, which can include external workshops, seminars, or in-house training resources.
Employees may also adapt to different software programs, leading to inconsistencies in design practices and output quality. With varying levels of expertise among team members, maintaining a uniform standard of work becomes more challenging. Thus, investing in continuous training is essential for realizing the potential benefits of CAD software, despite the challenges it presents.
End
The conclusion serves as a pivotal section in reinforcing the core arguments and insights presented throughout the article. It summarizes how the integration of factory CAD software has revolutionized modern manufacturing. Specifically, it highlights the efficiency gains in design processes, the accuracy enhancements in production, and the improvements in collaboration among teams.
In today's competitive landscape, CAD software is not merely an optional tool; it has become integral to maintaining relevance and operational success. It addresses a variety of manufacturing challenges, from promoting precision in designs to facilitating continuous communication among departments.
There are several key elements that the reader should take away:
- Efficiency: The ability of CAD software to streamline workflows significantly reduces the time required for design and production.
- Accuracy: Tools within CAD systems help minimize errors, ensuring that products meet specifications and standards.
- Collaboration: Enhanced communication features foster teamwork, which is vital for complex projects involving multiple stakeholders.
Furthermore, considerations about its implementation must not be understated. Organizations should approach CAD software integration thoughtfully, tailoring solutions to their unique needs. This involves assessing existing processes, conducting effective training programs, and considering costs versus benefits carefully.
"The right technology helps businesses stay ahead by optimizing their production capabilities."
Ultimately, the conclusion reaffirms the transformative potential of factory CAD software in manufacturing settings today. It allows businesses to adapt to changing market demands and technological advancements, positioning them for sustainable success.
Recap of Key Points
- The integral role of CAD software in enhancing design precision and accuracy.
- Improvements in production efficiency and cost reduction through streamlined processes.
- The importance of collaboration and effective communication in modern manufacturing settings.
- Key challenges such as high initial investment costs and the need for ongoing training.
- Future trends that include the integration of AI and cloud-based solutions.
Future Outlook for Factory CAD Software
The landscape of CAD software is rapidly evolving, poised to incorporate numerous innovative features that reflect technological advancements. Future developments may include a greater reliance on artificial intelligence, which has the potential to automate mundane tasks, streamline design processes, and even provide predictive analysis for production cycles. This could vastly enhance decision-making capabilities in manufacturing environments.
Further, cloud-based CAD solutions will cater to an increasingly mobile workforce, allowing for seamless access to software and data from virtually anywhere. This shift is expected to enhance collaboration across geographically dispersed teams. As manufacturers seek more flexible and adaptable solutions, the growth of cloud computing will undeniably play a significant role in shaping the future of CAD software.
In summary, the continuous advancement of factory CAD software promises not only to address present challenges but also to redefine the boundaries of what's possible in manufacturing. The future seems bright for those willing to embrace these innovative solutions, and organizations that strategically plan for these changes will likely remain at the forefront of their industries.