Optimizing Manufacturing with Order Management Systems
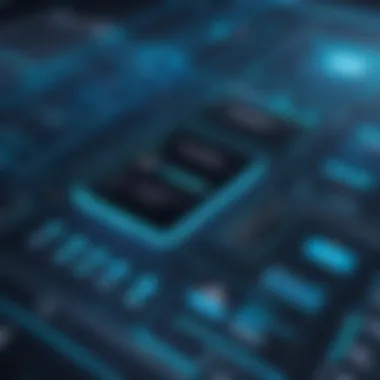
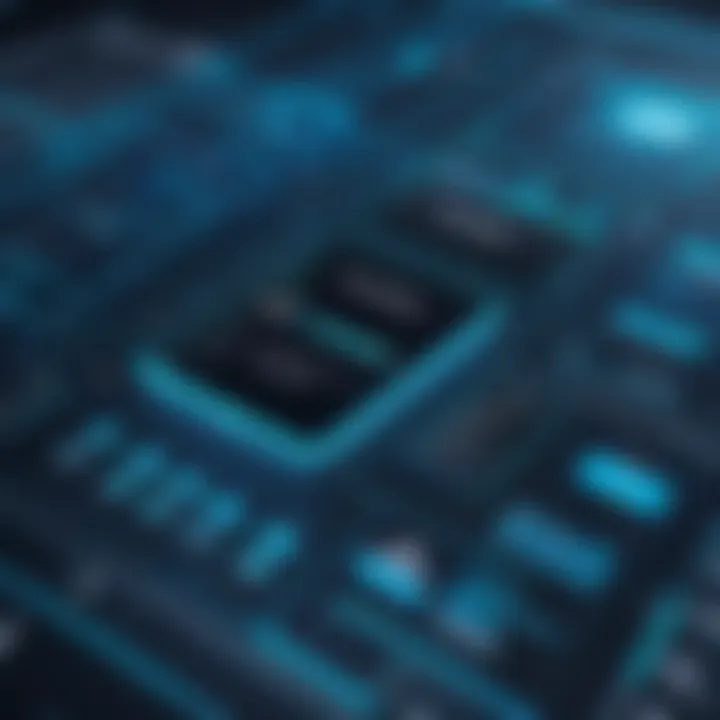
Intro
In today's fast-paced manufacturing environment, businesses are consistently striving for operational excellence. An Order Management System (OMS) acts as a backbone in this quest, facilitating smoother processes, improving tracking efficiencies, and enhancing communication across various departments.
As companies scale, the complexity of managing orders grows, leading to challenges that can significantly impact productivity and customer satisfaction. Without an effective OMS in place, manufacturers may find themselves grappling with delays, miscommunication, and inventory inaccuraciesâall of which can cause a ripple effect on their bottom line.
This article aims to provide a deep dive into the pivotal components of an OMS, emphasizing their role in manufacturing operations. It will explore essential features and technical aspects that drive performance and shed light on real-world user experiences, helping professionals identify the best solutions for their unique needs.
By the end, readers will gain a comprehensive understanding of how to harness the power of order management systems, enabling them to optimize their processes and align operations with their business objectives.
Prelude to Order Management Systems
In the dynamic world of manufacturing, an efficient order management system (OMS) is not just beneficial; it's essential. This system acts as the linchpin that holds various operations together, making it a critical area of focus for businesses aiming to optimize their processes. Efficient order management translates directly to improved productivity, enhanced customer satisfaction, and better inventory control. Without a proper OMS in place, manufacturers may find themselves swimming against the tide, struggling to keep pace with demand while managing supplies and inventory.
A well-implemented OMS centralizes order processing, from the moment a customer clicks that 'buy' button to the point of delivery. It ensures that every product is accounted for, tracked, and delivered punctually. As challenges in the manufacturing landscape continue to emergeâbe it fluctuating consumer demand, supply chain disruptions, or rising operational costsâthe necessity for a robust OMS cannot be overstated.
Understanding how this system integrates within manufacturing is vital for IT and software professionals, along with small and large businesses alike. It brings to light the fundamental elements that enhance efficiency, optimize resource allocation, and ultimately lead to sustainable growth. Also, grasping the nuances behind order management lays the groundwork for addressing common hurdles, such as implementation challenges or user resistance, which can derail even the best-laid plans.
The OMS is not merely a tool; it reflects the mindset of a manufacturing businessâits agility, customer focus, and drive for operational excellence. As we delve deeper, it will become clear why the role of an OMS is pivotal in navigating the complexities of modern manufacturing.
Definition and Purpose
An order management system is essentially a digital solution designed to streamline the entire order processing lifecycle. This begins with receiving and tracking orders to managing inventory and overseeing the fulfillment process. The primary goal is to ensure that every order is efficiently processed and delivered to the customer, maintaining the integrity of the supply chain. By automating routine tasks, an OMS minimizes human error, enhances visibility across operations, and ultimately drives productivity.
Key Features of an OMS Include:
- Order Processing: Automates order entry and updates.
- Inventory Management: Tracks stock levels and forecasts needs.
- Reporting and Analytics: Provides insight into sales trends and customer behavior enhancing decision-making.
- Integration Capabilities: Works seamlessly with other software like CRM systems and ERP solutions.
- Customer Communication: Keeps customers informed about their order status in real-time.
By integrating these features, manufacturers gain an edge in meeting their customers' demands quickly and efficiently.
Historical Context
To appreciate the modern OMS, it's essential to glance back at the evolution over the decades. Before the rise of digital solutions, many manufacturers operated on paper-based systems or rudimentary software, leading to significant inefficiencies.
In the early days, inventory was tracked manually. Orders were often lost, misplaced, or severely delayed, costing time and money. As manufacturing processes became more complex with globalization and increased competition, the need for an integrated approach became clear. The advent of information technology in the late 20th century marked a turning point, allowing for the development of comprehensive software that could address these complexities.
The introduction of barcode scanning and later, RFID technology, revolutionized how manufacturers tracked and managed inventory and orders. Throughout the 21st century, with the emergence of cloud-based solutions, manufacturers could implement OMS without the burdensome costs traditionally associated with on-premise systems.
"Order management systems have transitioned from simple tools to sophisticated systems that are indispensable for manufacturers seeking operational excellence."
With advances in technology, the potential of OMS continues to expand, integrating with AI and automation, paving the way for future innovations in the manufacturing sector.
Key Components of an Order Management System
In the world of manufacturing, an Order Management System (OMS) serves as the backbone of operational efficiency. The key components of an OMS function synergistically to create a seamless flow of information and processes. Each part plays a vital role in ensuring that customer orders are fulfilled accurately and timely, making this system indispensable in todayâs fast-paced business environment.
Order Processing Workflow
The order processing workflow is one of the most pivotal components of an OMS. It's the pathway that an order travels from creation to completion. Imagine a well-oiled machine where every cog has a place; that's how an effective order workflow operates.
The workflow typically begins with order placement, where customers place their orders through various channelsâbe it online, over the phone, or even in-person. Once the order is captured, the OMS automatically triggers a series of processes:
- Order validation: Checks if the product is available and the customer information is accurate.
- Picking and packing: Warehouse staff or automated systems retrieve the items from inventory.
- Shipping: Arrangements for delivery are made, and tracking information is generated.
This streamlined flow reduces human errors, accelerates processing times, and ultimately enhances the customer experience. Any hiccup in this workflow can lead to delays and dissatisfaction, making its optimization vital.
Inventory Management Integration
Another significant facet of an OMS is its integration with inventory management systems. Real-time inventory visibility is crucial in avoiding stockouts or overstock situations, which can severely impact operations and profits.
An effective OMS ensures that inventory levels are updated instantly whenever an order is placed or fulfilled. This synchronization allows manufacturers to know precisely whatâs on hand, what needs to be reordered, and whatâs been committed to customer orders. Here are a few elements to consider:
- Stock levels: Easily view quantities of raw materials and finished goods.
- Automatic reordering: Triggers orders to suppliers when stock drops below preset levels.
- Forecasting capabilities: Uses historical data to predict product demand, reducing excess inventory.
This level of integration not only keeps operations running smoothly but also supports better cash flow management by reducing excess inventory costs.
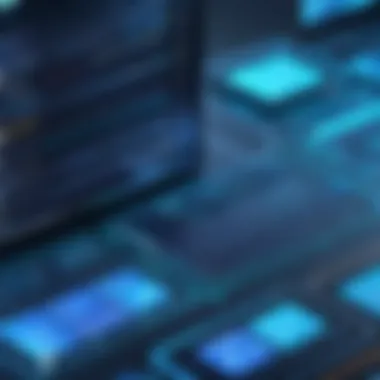
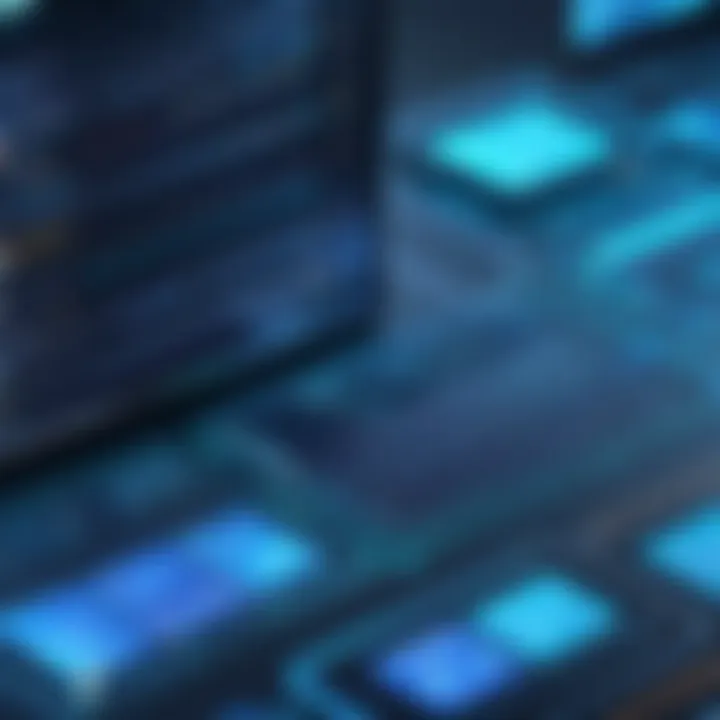
Customer Relationship Management (CRM) Features
The integration of CRM features in an OMS cannot be overlooked. A solid OMS helps create a richer customer experience by leveraging customer data collected throughout the order lifecycle.
When customers interact with a manufacturing brand, they expect personalized service and quick responses. An OMS equipped with CRM capabilities can:
- Track customer interactions: Understand the history of customer purchases and preferences.
- Facilitate communication: Automate notifications about order status, shipping updates, and even promotional offers.
- Gather feedback: Collect customer responses post-purchase, which can be crucial for refining products and services.
"Understanding customer patterns is like having a compass that directs you towards the best business decisions."
Integrating CRM features allows for better customer loyalty and aids businesses in adapting to customer needs swiftly, boosting overall satisfaction.
The Importance of Real-Time Data
In the fast-paced world of manufacturing, the significance of real-time data cannot be overstated. It serves as the backbone of effective order management systems, enabling businesses to respond swiftly to market changes, manage resources judiciously, and meet customer expectations with remarkable agility. Without timely and accurate data, organizations might find themselves like ships lost at seaâlacking a compass to navigate the tricky waters of supply and demand.
Real-Time Tracking
One of the prime benefits of real-time data lies in its capability for tracking orders meticulously throughout their lifecycle. When manufacturers have their fingers on the pulse of their operations, they can pinpoint exactly where an order standsâwhether itâs still in the queue, being processed, or en route to the customer. This level of transparency not only satisfies internal stakeholders but also builds trust with customers who expect timely updates.
For example, when a plant uses systems that provide real-time visibility into inventory or order status, it eliminates the anxiety associated with uncertainty. Customers can be promptly informed of delays or changes, allowing them to adjust their expectations accordingly. This clear communication is vital, as it significantly enhances customer satisfaction.
Additionally, access to real-time data helps in identifying bottlenecks. If one part of the order process lags behind, managers can take swift actions to mitigate delays. This could involve allocating resources differently or adjusting workflows. The adage "a stitch in time saves nine" rings particularly trueâearly identification of issues often prevents larger complications later on.
Demand Forecasting
The role of real-time data extends beyond mere tracking; it is instrumental in effective demand forecasting. With current data in hand, businesses can analyze trends and predict future demand with a fair degree of accuracy. This capability is akin to possessing a crystal ballâallowing manufacturers to anticipate spikes or drops in demand driven by seasonal shifts or market fluctuations.
Consider a scenario where a manufacturer relies on historical data alone. If a sudden increase in demand occurs due to an unexpected trend, they might face stockouts or overproduction, both of which can be detrimental. Conversely, utilizing real-time data enables the fine-tuning of inventory levels and production schedules, aligning them closely with actual market needs.
In light of this, employing advanced analytics tools that harness real-time data can significantly improve forecasting accuracy. According to industry reports, businesses that effectively leverage real-time insights see a marked improvement in their operational efficiency and cost reduction.
"Adaptability to demand changes is not just an advantage; it's a necessity in today's manufacturing landscape."
Ultimately, the integration of real-time data into order management systems cannot be viewed as a mere enhancementâit is a fundamental necessity for any manufacturing entity aiming for longevity and relevance in a competitive market. The ability to not only track orders but also anticipate demand empowers organizations to operate with foresight and precision.
Benefits of an Effective OMS in Manufacturing
The implementation of an Order Management System (OMS) in manufacturing brings about several key benefits that can profoundly impact operational success. These advantages extend beyond simple administrative tasks, revolutionizing the entire workflow, and ensuring a more agile and responsive business environment. In an arena where precision and timing are paramount, an effective OMS serves as a backbone, enabling manufacturers to navigate the complexities of order processing with confidence. Below, we will delve into three core aspects that highlight the benefits of an effective OMS.
Enhanced Efficiency
When it comes to efficiency, an effective OMS can often feel like a well-oiled machine. By automating repetitive tasks and streamlining processes, it reduces manual intervention, leading to significant time savings. For instance, automation of order entry and processing tasks minimizes the likelihood of human error and frees up employees to engage in more strategic functions rather than getting bogged down in paperwork.
Moreover, the integration of the OMS with supply chain management systems enables real-time access to critical data. This means that as soon as an order is placed, all relevant parts of the operation are notified immediatelyâfrom inventory levels and manufacturing schedules to shipping logistics. This level of coordination means that bottlenecks can be identified and resolved faster.
"Incorporating an effective OMS leads to speedier operations, more predictable outcomes, and less guesswork throughout the workflow."
Improved Accuracy
With accuracy, the stakes are high. A single mistake in order fulfillment can lead to lost customers and wasted resources. An effective OMS minimizes errors through various means. First, by utilizing barcode scanning and RFID technology, accuracy in tracking inventory is significantly enhanced. Orders are tracked with greater precision, from the moment they are received to when they are delivered. This meticulous tracking not only decreases the likelihood of errors but also provides an audit trail for accountability.
Additionally, real-time inventory updates prevent oversellingâone of the common pitfalls in manufacturing. This responsibility to keep information accurate means businesses are less likely to deal with backorders or mismatched stock levels, which can plague customer satisfaction. The operating principle here is simple: the more dynamic and correct your data, the more reliable your operations become.
Better Customer Satisfaction
At the heart of every business is the customer experience. An effective OMS contributes significantly to customer satisfaction by ensuring clearer communication and faster response times. When orders are processed seamlessly, customers are informed at every stageâwhether itâs order confirmation, shipment tracking, or delivery notifications. This transparency builds trust and loyalty.
Moreover, timely deliveries and accurate orders naturally lead to happier customers. In turn, satisfied customers are more likely to become repeat clients, positively affecting bottom-line profits. Companies that leverage an effective OMS often find they can serve larger volumes of orders without sacrificing qualityâit's a balancing act that becomes easier with robust systems in place.
Challenges in Implementation
Implementing an Order Management System (OMS) in manufacturing is akin to navigating a ship through stormy seas. There are potential pitfalls aplenty, and each requires careful consideration. Addressing these challenges head-on not only ensures a smoother transition but also maximizes the system's potential. Letâs dive deeper into the critical issues: resistance to change, costs of integration, and training needs.
Resistance to Change
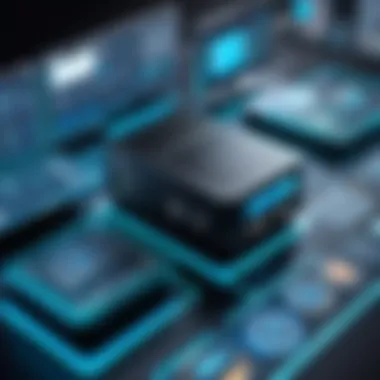
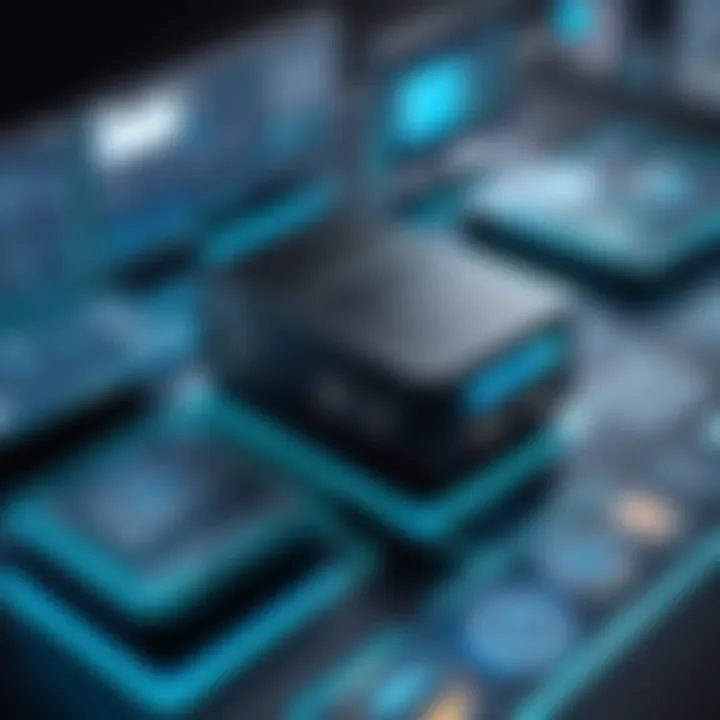
Humans are creatures of habit, and in the realm of manufacturing, this is particularly evident. When new systems are introduced, there often exists a reluctance among employees to embrace these changes. Many may feel comfortable with existing workflows, believing them to be sufficient. This reluctance can lead to a poor adoption rate, jeopardizing the efficiency gains intended by the new OMS.
To mitigate this, effective change management strategies are essential. Involve team members early in the process. Gather their insights and address concerns openly. Providing clear communication about the benefits can foster a more welcoming environment.
- Transparent Communication: Regular updates and transparency around the implementation process can bolster trust among staff.
- Involve Employees: Bringing key stakeholders to the discussion can create a sense of ownership, easing the transition.
"Resistance often stems from a place of uncertainty. Tackle this by ensuring everyone knows whatâs in it for them."
Cost of Integration
An important aspect to consider is the financial investment involved in the integration of an OMS. Costs can accumulate swiftly, from software fees to potential infrastructure upgrades. Many manufacturing firms find themselves at a crossroads: invest now for long-term benefits or tighten budgets in the short term?
While the initial costs may seem daunting, itâs crucial to evaluate the long-term return on investment. Consider how the new OMS may reduce operational inefficiencies or enhance customer satisfaction through timely deliveries.
- Upfront Costs: Initial software purchase, licenses, or subscriptions can be significant.
- Operational Disruption: Temporarily halting existing processes during implementation can result in lost revenue.
Taking a strategic approachâassessing potential cost savings and efficiency improvementsâcan alleviate some of the financial burdens.
Training Requirements
Lastly, but certainly not least, is the training that will be necessary to enable staff to effectively leverage the new system. Without proper training, even the most sophisticated OMS can become a point of frustration rather than a tool for enhancement.
Training should be structured, addressing the varying levels of tech-savvy among employees. Customized sessions can improve engagement. Incorporating hands-on learning through workshops or practical simulations can significantly enhance understanding and retention.
- Customized Training Programs: Tailoring training to different user groups, from managers to floor staff, can facilitate smoother onboarding.
- Ongoing Support: Post-implementation training ensures that staff continuously improve their skills, adapting to system updates as they arise.
Software Options for Order Management
In the world of manufacturing, the right order management system (OMS) can act like the oil that keeps a finely tuned machine running smoothly. As businesses strive for efficiency and accuracy, understanding the software options available for order management becomes crucial. These options not only dictate the workflow but also determine how well a company can adapt to market changes and customer demands. Selecting the correct system has tangible benefits, including streamlined operations, reduced errors, and enhanced customer interaction. But itâs not just about picking a software that looks good on paper; considerations such as cost, scalability, and integration with existing processes play a pivotal role.
When we dive into the two primary software optionsâcloud-based solutions and on-premise systemsâthe road may divide, but both paths can lead to success if chosen wisely. Letâs take a closer look.
Cloud-Based Solutions
Cloud-based order management systems have skyrocketed in popularity, and for good reason. They are often perceived as the go-to option for modern-day manufacturing due to their flexibility and accessibility. Imagine having the power to monitor your inventory and orders from any location, thanks to the internetâthis isnât a pipe dream; it's the reality with cloud-based solutions.
Advantages:
- Scalability: You can easily scale up or down based on your business needs without costly infrastructure changes.
- Cost-Effective: Generally, these solutions work on a subscription basis, which means lower initial costs.
- Automatic Updates: Software continually receives updates from the provider, eliminating worries about maintaining the software.
- Collaboration: Teams can collaborate seamlessly, as information is real-time and accessible from multiple devices,
However, itâs not all sunshine and rainbows. There are challenges too. For instance, businesses may have concerns regarding data security since they rely on third-party service providers. Moreover, internet connectivity is crucial; a lagging connection can significantly impact productivity.
On-Premise Systems
On-premise systems, on the other hand, bring a different flavor to the table. These systems are installed locally on a companyâs servers, and many businesses prefer them for the control they offer over their data. Companies with stringent data compliance requirements, such as those in the aerospace or pharmaceutical sectors, may find on-premise solutions to be more suitable.
Advantages:
- Data Control: Businesses have full control over their servers and data, which is reassuring for companies worried about cloud vulnerabilities.
- Customization: On-premise systems often allow for greater customization to fit the specific needs of a manufacturing operation.
- One-Time Fees: While initial costs may be high, over time these systems can be more affordable than ongoing cloud subscriptions.
However, potential downsides loom, primarily concerning maintenance and updates, which fall squarely on the company. A business must have the talent and resources dedicated to this, which can prove to be more costly in the long run.
In summary, choosing between cloud-based solutions and on-premise systems ultimately hinges on the specific needs of each manufacturing operation. Decision-makers should weigh the benefits and considerations unique to their circumstances. For professionals seeking effective order management, understanding these software options isn't just beneficial; it's essential.
"Selecting the right order management software can define how well a business meets its customers' expectations."
Whether itâs advanced scalability of cloud-based systems or the robust control offered by on-premise solutions, the right choice will pave the way for future growth and operational excellence.
User Experiences and Case Studies
In today's highly competitive manufacturing landscape, the integration of Order Management Systems (OMS) is essential not just for streamlining processes, but also for ensuring that companies meet customer demands effectively. User experiences and case studies play a pivotal role in demonstrating the tangible benefits of these systems and shedding light on practical applications that go beyond theoretical knowledge. By examining real-world scenarios and feedback from users, businesses can glean insights that inform decision-making and operational strategies.
Importance of User Experiences
Understanding how different organizations utilize OMS is key for several reasons:


- Practical Insights: Real-world experiences provide a view of how various features perform under specific conditions.
- Performance Benchmarks: Case studies reveal success stories that can serve as performance benchmarks for prospective users.
- User Feedback: Insights into user satisfaction and challenges can inform software development and help tailor solutions to meet market needs.
Utilizing these experiences can foster an environment of continuous improvement within manufacturing processes. When companies share their results, it not only helps to establish industry standards but also encourages innovation among peers.
Case Study: Company A
Company A, a mid-sized electronics manufacturer, recently implemented an OMS to combat inefficiencies in their order processing workflow. Before integrating the new system, their team dealt with numerous challenges related to order tracking and inventory management. Delays were common, which led to dissatisfied customers and increased operational costs.
After deploying the OMS, the results were remarkable. The order tracking capabilities provided real-time updates that allowed the staff to address issues proactively instead of reactively. Inventory management was seamless; the system automatically updated stock levels, reducing instances of backorders and improving the customer experience.
The most significant takeaway from Company A's experience was the enhanced visibility offered by the OMS. Employees could view the entire order lifecycle, enabling better communication across departments. As a result, lead times decreased significantly, and overall customer satisfaction improved remarkably. This case study highlights that implementing an effective OMS is more than just a technical upgradeâit is a transformation of company culture towards a more transparent and efficient operation.
User Feedback on Various Platforms
User feedback from various platforms provides an essential perspective on the effectiveness of different OMS solutions. Platforms such as Reddit and specialized forums house discussions where users share their detailed experiences, alongside the pros and cons of specific systems.
The feedback generally highlights areas including:
- Ease of Use: Many users emphasize how intuitive a system is or the absence of a steep learning curve can positively influence implementation success.
- Integrations: The capability of the system to integrate with existing software is often discussed. Users appreciate platforms that easily connect with CRM tools or ERP systems, making transitions smoother.
- Support Services: Comments on customer support quality often surface, as timely assistance can be critical, especially during initial setup.
"It's crucial to listen to what actual users are saying. They often point out quirks and features that marketing materials gloss over."
In summary, engaging with user experiences and case studies is not just beneficial; it's an essential practice for businesses looking to adapt and prosper in their order management strategies. By learning from the successes and pitfalls of others, manufacturers position themselves to make informed decisions that can lead to substantial gains.
Future Trends in Order Management Systems
As we step into an era marked by rapid technological advancements, the future of Order Management Systems (OMS) for manufacturing is becoming increasingly significant. Envisioning how these systems will evolve gives businesses the upper hand for staying competitive. By embracing the right trends, manufacturers can not only drive efficiency but also enhance their overall operational insight. Some critical aspects worth examining include the integration of automation and artificial intelligence, as well as the development of more user-centric interfaces.
Automation and AI Integration
Automation paired with AI is reshaping the foundations of manufacturing. It isn't just about cutting down manual tasks; it's about streamlining the entire order lifecycle. By using AI in an OMS, manufacturers can analyze vast amounts of data in real time, predicting demand more accurately and adjusting inventory levels accordingly.
Here's how this combo can elevate performance:
- Informed Decision-Making: AI analyzes patterns in customer behavior and order history, allowing manufacturers to make intelligent decisions that minimize errors and maximize productivity.
- Predictive Analysis: Anticipating demand is crucial. Integrating AI can assist in forecasting by processing historical data and market trends to suggest timely adjustments in production.
- Efficiency in Workflow: Automation takes over repetitive tasks. When orders need to be processed or invoices generated, automating these workflows means staff can focus on strategic initiatives instead of getting bogged down in menial tasks.
One cannot overlook the potential cost savings that come with this shift. While the initial investment may raise some eyebrows, the long-term returns can far outweigh the upfront costs.
Enhanced User Interfaces
Another trend gaining traction is the focus on enhanced user interfaces. A system may have all the bells and whistles, but if itâs tricky to navigate, users will find it frustrating. A clean and intuitive interface dramatically improves user experience and, consequently, increases the likelihood of successful implementation.
Consider these features:
- Custom Dashboards: Giving users the ability to customize their dashboards can lead to quicker access to the information they need.
- Mobile Compatibility: With the ever-increasing use of mobile devices, ensuring that OMS can be accessed and managed via smartphones or tablets is becoming a necessity. Operational flexibility often translates to efficiency.
- Seamless Integration: A good user interface integrates easily with other software tools, from customer relationship management to supply chain logistics, allowing data to flow smoothly.
In a nutshell, enhanced user interfaces pave the way for more widespread adoption of OMS in the manufacturing sector. As the old saying goes, âYou donât get a second chance to make a first impression.â The challenges faced by users, if not addressed, can potentially hamper the benefits of an otherwise sophisticated software system.
"The future of seamlessly connected systemsâwhere AI meets user designâcould transform the manufacturing landscape, leading to unprecedented efficiency."
Understanding these future trends is not just about predicting changes, but about preparing the ground for sustained growth and adaptation. Manufacturers that invest in these technologies today will likely leverage their innovations to thrive in tomorrow's competitive marketplaces.
Culmination
This article has illuminated the critical role of order management systems (OMS) in the manufacturing landscape. Emphasizing efficiency and accuracy, an OMS serves as a backbone, streamlining processes in a way that can be likened to a conductor orchestrating a symphony. Each segment of the order lifecycle, from initiation to fulfillment, relies on precise coordination, which an effective OMS facilitates.
The benefits of implementing a robust OMS are manifold. First and foremost, enhanced efficiency is a significant advantage, enabling businesses to optimize resource allocation and reduce cycle times. Additionally, the integration of real-time data ensures that operations are not only reactive but also proactive, allowing companies to adapt swiftly to market demands. This gets underlined by the emphasis on data accessibility, where decision-making can thrive on solid intel rather than guesswork.
Beyond operational benefits, thereâs also a notable improvement in customer satisfaction. When orders are processed more accurately and delivered on time, trust builds between manufacturers and their customers. A solid OMS lays the groundwork for a positive reputation, which is invaluable in today's competitive arena.
While the implementation can come with its own set of challengesâlike resistance to change or the costs of new technologyâunderstanding these hurdles is the first step to addressing them effectively. Businesses must weigh the upfront investments against the long-term gains to appreciate that a well-integrated OMS is not merely a software tool but a strategic ally.
As we draw this discussion to a close, it is evident that the potential of order management systems extends far beyond basic functionality. They are essential not only for managing orders but for shaping the future of manufacturing practices, and thus, it is crucial for businesses to invest in systems that are equipped to meet expected demands and adapt to future needs.
Summary of Key Points
- Efficiency improvements: Streamlined processing leads to faster order delivery.
- Real-time data integration: Allows for timely adjustments based on current conditions.
- Customer satisfaction uplift: Reliable order management instills customer trust and loyalty.
- Challenges in implementation: Understanding resistance and integration costs is essential for a smooth transition.
Final Thoughts
In summary, as companies continue to navigate an ever-evolving manufacturing environment, the importance of a comprehensive order management system cannot be understated. Considerations for future developments should include automation and artificial intelligence advancements, enhancing user interfaces, and integrating new technology for improved performance.
By prioritizing these elements, manufacturing firms not only address current operational needs but also set the stage for sustainable growth and agility, ensuring they are well-equipped to face the future challenges that lie ahead. In doing so, businesses can harness the full potential of their functional and competitive strengths.