Companies Demonstrating Outstanding Quality Management
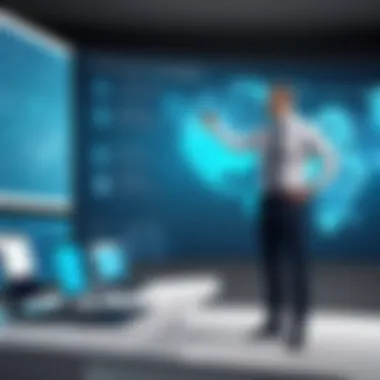
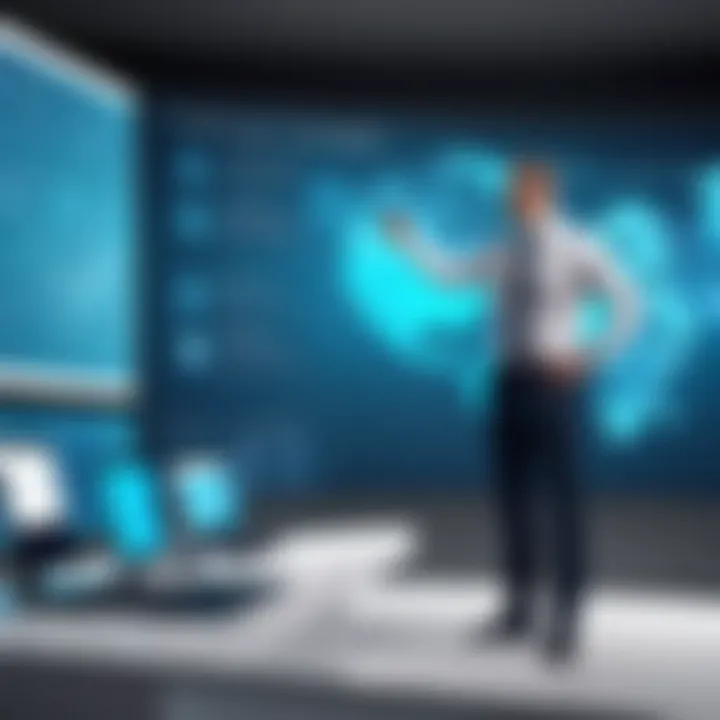
Intro
Quality management plays a crucial role in any business’s success, regardless of its size or industry. Organizations that prioritize quality management strategies lever achieve higher operational efficiency and customer satisfaction. It’s more than just controlling processes or adhering to standards; it’s about creating a culture of excellence that permeates every level of the organization.
In this article, we’ll explore several companies that have not merely adopted quality management practices but have truly integrated them into their core operations. We will look at what makes their approaches stand out and how they have reaped tangible benefits. From renowned global corporations to promising startups, these examples provide a rich tapestry of methodologies and philosophies.
We will delve into underlying principles of quality management, such as the importance of leadership commitment and the drive for continuous improvement. We will also discuss how a positive workplace culture and meaningful employee engagement can significantly impact quality outcomes. This provides a unique opportunity to glean insights that can be applied in similar contexts, whether in IT firms or traditional manufacturing setups.
Companies Showcasing Distinct Quality Practices
While numerous organizations might boast of quality measures, only a handful have managed to achieve and sustain world-class status. Each has its own story to tell, underscoring that there is no one-size-fits-all in quality management.
Toyota: The Pioneer of Lean Manufacturing
A household name in the automotive industry, Toyota is often hailed as the gold standard for quality management. Through its famous Toyota Production System (TPS), the company emphasizes waste reduction, continuous improvement, and respect for people.
"The Toyota Way emphasizes long-term thinking over short-term goals, ensuring that the company remains resilient in the face of adversities."
Their Kaizen philosophy—small, continuous improvements—has been an influential model in industries around the world.
Amazon: Customer-Centric Focus
With quality management deeply enshrined in its customer promise, Amazon exemplifies how integrating customer feedback into the core of operations drives quality. Their use of technology to enhance logistics and customer service ensures high standards in fulfillment and customer experience.
Apple: Innovation Through Quality
Apple’s reputation lives and breathes quality, from product design to user experience. The company's rigorous control and testing processes ensure that products reach consumers in prime condition. Apple’s brand loyalty can largely be attributed to its quality ethos, fostering a devoted customer base.
Synthesizing the Insights
The examination of these exemplary companies reveals crucial takeaways for other businesses aiming to enhance their own quality management practices. Prioritizing customer satisfaction, engaging employees, and fostering a culture of continuous improvement are integral to achieving high-quality standards.
Businesses can look at these models not just as end goals but as ongoing journeys—one that requires commitment and adaptability. Quality management is not merely an operational necessity; it can be a strategic advantage that leads to sustained success and growth.
Foreword to Quality Management
Quality management is not just a buzzword; it’s a crucial linchpin that can dictate the fate of an organization. In a world where competition is fierce and the demand for excellence is sky-high, understanding and implementing effective quality management is essential. Companies that prioritize quality tend to thrive, garnering customer loyalty while reducing waste and operational inefficiencies.
Defining Quality Management
Quality management encompasses the processes, systems, and practices that an organization employs to ensure the quality of its products or services. At its core, it revolves around a commitment to delivering high standards consistently. It's about identifying customer requirements, setting quality objectives, and continually assessing how well an organization meets them. When unraveling the components of quality management, we often find three key pillars: quality planning, quality assurance, and quality improvement.
- Quality Planning involves defining the desired level of quality and the processes necessary to achieve it.
- Quality Assurance ensures that quality requirements are met throughout production or service delivery.
- Quality Improvement focuses on enhancing the processes overtime.
All in all, quality management is about creating a culture wherein each department and employee understands their role in maintaining high standards.
Importance of Quality Management in Business
In today’s business landscape, the importance of quality management can’t be overstated. Consider the potential repercussions of overlooking quality standards: dissatisfied customers, damaged reputations, and lost revenue.
Key Benefits of Quality Management:
- Customer Satisfaction: Products that meet or exceed expectations can foster loyalty, transforming customers into advocates.
- Operational Efficiency: Streamlined processes reduce waste, leading to cost savings.
- Risk Management: With robust quality management, organizations can identify and mitigate risks proactively.
- Competitive Advantage: Businesses renowned for quality can differentiate themselves from rivals in crowded markets.
"The road to success is paved with quality. Excellence is not a skill, it’s an attitude."
Clearly, the alignment of quality objectives with business strategies can not only enhance performance but also contribute to an enriched corporate culture. Companies are beginning to realize that quality management is not merely a department’s responsibility but is woven into the very fabric of the organization. As we dive deeper into this article, examples of outliers that excel at these practices will surface, providing insights into successful quality management frameworks.
Historical Context of Quality Management
Understanding the historical context of quality management is crucial for grasping how current practices have evolved and why certain methodologies are embraced over others. Quality management is not just a modern concept; it has roots in industrial practices and philosophies that date back to the early 20th century. By dissecting this evolution, one can appreciate the significant milestones that have shaped today’s quality standards and methodologies.
Historically, the focus on quality was often reactionary, responding to failures and defects. Companies saw quality as a control mechanism rather than an integral part of their systems. This led to the development of quality checks at the end of production lines, where products were inspected for conformity to standards. However, as industries expanded, the limitations of this reactive approach became apparent. Companies faced not only competition but consumer demand for better, more reliable products. This shift was pivotal in pushing organizations to adopt proactive quality practices.
Evolution of Quality Management Practices
Quality management has undergone various transformations throughout the years. Initially, the early quality control practices revolved around statistical methods that aimed to mitigate errors and waste. Notably, the introduction of statistical quality control during the 1920s laid the groundwork for a more structured approach to quality measurement. The work of Walter A. Shewhart established the foundations for control charts, which are now standard tools used in quality control processes.
As we moved into the mid-20th century, individuals like W. Edwards Deming and Joseph Juran began advocating for a broader view of quality that included every aspect of an organization’s operations. Deming's principles emphasized the continuous improvement of processes, fostering a shift from mere inspection to embedding quality into the organizational culture. Companies learned to view quality as a holistic feature that must involve management, employees, and suppliers.
The latter part of the century saw the emergence of Total Quality Management (TQM) initiatives, which further reinforced the idea that quality is everyone’s job. The practices laid down during this period, including the focus on customer satisfaction and employee engagement, radically transformed how businesses operate today. Lean principles also emerged, advocating for efficiency while still maintaining quality standards. The evolution continued, adapting to technological advancements and changing consumer expectations.
Influential Figures and Their Contributions
The narrative of quality management would be incomplete without mentioning influential figures who contributed to its framework. W. Edwards Deming, for instance, revolutionized quality management with his famous PDSA (Plan-Do-Study-Act) cycle, promoting ongoing improvement and data-driven decision-making.
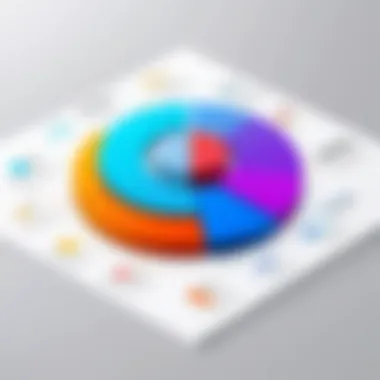
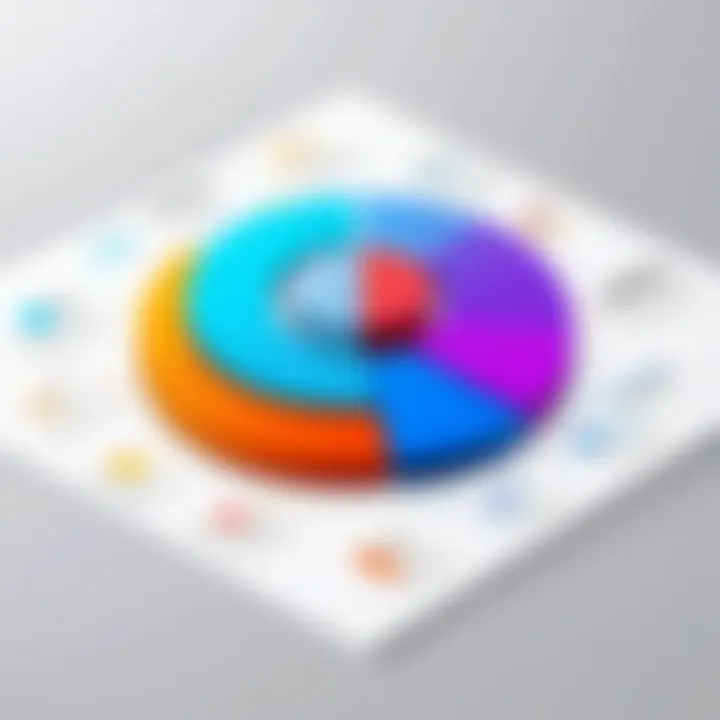
"Quality comes not from inspection, but from the improvement of the process."
– W. Edwards Deming
Another pivotal figure is Kaoru Ishikawa, whose development of quality circles encouraged teamwork and the use of cause-and-effect diagrams, often referred to as Fishbone diagrams, to improve problem-solving in processes. He believed that all employees should have a role in improving quality, which resonated strongly with the principles of participation and collaboration.
Joseph Juran's Quality Trilogy, which includes planning, control, and improvement, also holds a vital place in the quality management lexicon. His emphasis on understanding the cost of poor quality and how it affects business outcomes changed the way businesses reconciled quality with profit. His work established the importance of setting quality goals that align with business goals.
The contributions of these individuals not only helped define quality management in their times but also laid down a legacy that companies continue to draw from. Understanding their impact provides insight into how quality management practices were not only formed but also why they have remained resilient in the face of changing business landscapes.
Fundamental Principles of Quality Management
Understanding the fundamental principles of quality management is essential for organizations aspiring to reach new heights in operational excellence. These principles are like the backbone of effective quality management systems. They guide companies in navigating the complexities of delivering high-quality products and services, ensuring consistency and customer satisfaction. Each principle provides a foundation upon which organizations can build their quality strategies to align with overall business objectives.
Customer Focus
A pivotal aspect of quality management is maintaining a tight focus on the customer. Companies that excel in this area, such as Procter & Gamble, employ strategies that enable them to listen attentively to customer feedback. This commitment to understanding and prioritizing the customer experience leads to higher satisfaction levels and fosters loyalty. It's not just about delivering what customers want but striving to exceed their expectations at every touchpoint. Companies can achieve this through:
- Regular surveys and feedback channels
- Utilizing data analytics to track consumer behavior
- Tailoring products based on direct customer insights
When organizations actively incorporate customer feedback into their processes, they build a solid foundation for continuous improvement.
Leadership Commitment
Quality management thrives when backed by strong leadership commitment. Leaders must embody the values of quality, promoting a culture where excellence is expected at every level. Toyota, known for its Lean manufacturing techniques, exemplifies this principle. Leadership at Toyota emphasizes:
- Active involvement in quality improvement initiatives
- Setting clear quality goals and measurable objectives
- Encouraging open communication about quality issues
When leaders commit to quality, they inspire their teams to take ownership of their roles. This proactive stance leads to a better-aligned workforce and long-term success.
Engagement of People
Engaging employees in the quality management process is essential. An organization can only be as strong as its people. Companies that recognize this, like Elia Group, emphasize collaborative environments where every employee feels valued. Effective strategies for enhancing engagement include:
- Regular training programs to upskill employees
- Incentive programs that reward contributions to quality efforts
- Establishing teams focused on quality metrics
Such initiatives create a sense of ownership and accountability among staff, leading to enhanced performance and a drive for improvement.
Process Approach
A clear understanding of processes is integral to successful quality management. This approach encourages organizations to examine their operational flows to identify areas for improvement. For example, using the process approach involves:
- Mapping out workflows and identifying bottlenecks
- Establishing key performance indicators to measure efficiency
- Employing tools like Six Sigma for process optimization
By adopting a process-centric outlook, organizations can streamline operations, minimize errors, and deliver consistent results.
Improvement Focus
Lastly, a relentless focus on improvement is vital for sustaining quality management practices. Rather than becoming complacent, leading firms continuously seek to enhance their practices and outcomes. Companies often implement:
- Regular assessments of quality management systems
- Initiatives that promote innovative thinking for solving quality issues
- Benchmarking against industry standards to gauge progress
A commitment to improvement not only drives quality but also prepares organizations to adapt to changing market demands and technologies.
"Quality is not an act, it is a habit." – Aristotle
In summary, mastering these fundamental principles equips organizations with the tools needed to refine their quality management systems effectively. By focusing on the customer, fostering leadership commitment, engaging employees, adopting a process approach, and committing to continuous improvement, companies can achieve and sustain high levels of quality that resonate throughout their operations.
Key Quality Management Methodologies
In the dynamic corporate landscape, where change is the only constant, effective quality management methodologies are paramount for organizations aspiring to maintain their competitive edge. By implementing structured approaches like Six Sigma, Total Quality Management (TQM), and Lean Management, companies can foster a culture that prioritizes quality across all functions. These methodologies not only help in streamlining processes but also in enhancing customer satisfaction and operational efficiency. Understanding these methodologies provides businesses with insights on how to elevate their quality management practices.
Six Sigma
Six Sigma is all about minimizing defects and reducing variability in processes. It’s a data-driven approach that equips organizations with techniques and tools for process improvement. By focusing on objectives and outcomes, Six Sigma helps pinpoint inefficiencies that can cost a business both time and money.
The methodology stands out for its structured framework known as DMAIC, which stands for Define, Measure, Analyze, Improve, and Control. This sequence ensures that any improvement initiative is based on solid data and analysis rather than guesswork. Implementing Six Sigma can lead to remarkable improvements in quality and efficiency, as well as significant cost savings.
Organizations that adopt this method not only bolster their operational processes but also improve their product or service quality. For example, a manufacturing company might utilize Six Sigma to refine its production cycle, ultimately resulting in fewer product defects and increased customer satisfaction.
Total Quality Management (TQM)
On the other hand, Total Quality Management (TQM) takes a more holistic approach to quality. TQM emphasizes that quality is everyone's responsibility, permeating all levels of an organization. It encourages a culture where employee engagement is vital for achieving excellence.
The principles of TQM include customer focus, continuous improvement, and a strategic approach to quality that incorporates every function of the organization. This contrasts with other methodologies that might focus mainly on processes or output. In TQM, all employees are trained to identify potential quality issues and suggest improvements.
Implementing TQM can be revolutionary; a study might reveal that a company like Ford, once plagued by quality issues, turned itself around by fostering a culture of quality through TQM. By engaging its workforce and focusing on customer satisfaction, it was able to enhance both service and loyalty among its clientele.
Lean Management
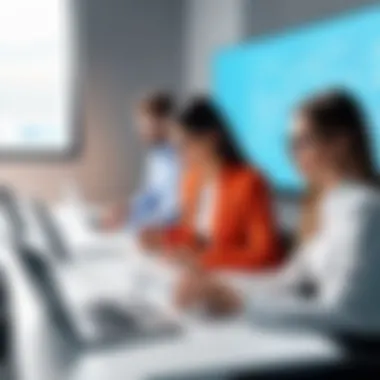
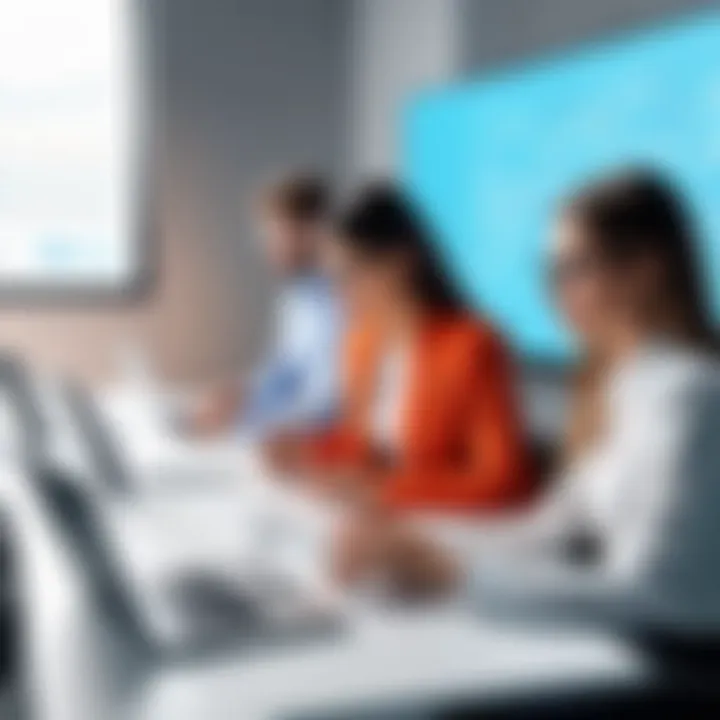
Finally, Lean Management is a methodology heavily rooted in the manufacturing sector but applicable across various industries. Lean focuses on maximizing value for customers while minimizing waste. The concept encourages a mindset of continuous improvement and efficiency.
Practicing Lean management involves mapping out value streams, identifying non-value-adding activities, and systematically eliminating these wastes. For instance, a software development firm could implement Lean principles by streamlining its coding processes, which could lead to quicker release times and less resource consumption.
In essence, Lean management cultivates an agile and responsive organization. Companies that leverage Lean practices often find themselves better equipped to adapt to change, which is increasingly crucial in today’s swift-moving market.
"Quality is never an accident; it is always the result of intelligent effort.” — John Ruskin
Establishing a Quality Management System
Establishing a solid quality management system (QMS) is a mission-critical part of any business aiming for long-term success. It creates a structured approach for meeting customer expectations and regulatory requirements. In today’s fast-paced market, businesses can’t afford to overlook the establishment of a QMS. It’s crucial not just for compliance, but also for fostering a culture of continuous improvement.
One of the primary benefits of a QMS is the enhancement of efficiency. When everyone is on the same page, processes are streamlined, mistakes are minimized, and resources are used more wisely. A well-implemented QMS can lead directly to a boost in customer satisfaction, as products and services become more reliable. Additionally, it paves the way for improved employee morale; when team members understand the processes and their roles within a system, engagement levels typically increase.
The considerations for establishing a QMS include selecting the right framework, ensuring commitment from leadership, and addressing potential cultural hurdles within the organization. Ultimately, the goal is to create a robust, flexible system that can adapt to ongoing changes in the business environment.
"A great QMS not only assures quality; it builds confidence."
Steps for Implementation
Implementing a quality management system requires a systematic approach. Here are some recommended steps that organizations might follow:
- Define the Scope: Clearly outline the reach and boundaries of the QMS within the organization. Understanding where it will apply is essential for effective implementation.
- Engage Leadership: It’s crucial to get commitment and support from top management. They play a pivotal role in setting the tone and direction of the QMS.
- Conduct a Gap Analysis: Analyze current processes and identify gaps that need addressing. This will provide a clearer picture of what’s working and what’s not.
- Document Processes: Use clear documentation to map out existing processes. This documentation should be easily accessible to all team members.
- Train Employees: Provide comprehensive training to all employees about the new processes. They need to understand their roles in the QMS to ensure successful adoption.
- Monitor & Review: After implementation, it’s vital to establish a regular review mechanism to assess the system's effectiveness and make necessary adjustments.
Measuring Quality Performance
Once a QMS is in place, measuring its performance is essential for continuous improvement. Quality performance metrics can take various forms and should be tailored to the organization's specific goals. Commonly used methods include:
- Customer Satisfaction Surveys: Employing direct feedback from customers helps gauge their satisfaction levels regarding products or services.
- Key Performance Indicators (KPIs): These metrics can include production efficiency, defect rates, and compliance levels. KPIs provide quantifiable measures that can be tracked over time.
- Internal Audits: Regular audits allow organizations to evaluate processes against standards, ensuring compliance and identifying areas for improvement.
- Employee Feedback: Engaging team member insights can unearth valuable information about the effectiveness of the QMS. Employees are often the best source for identifying inefficiencies in processes.
- Benchmarking: Comparing performance against industry standards or best practices can help organizations identify areas that need enhancement.
By systematically addressing these areas, companies can ensure their QMS not only meets current needs but also positions them well for future challenges. A focus on the holistic performance of the quality management system fosters an environment where quality is not just an afterthought, but a core company value.
Companies with Exemplary Quality Management
Quality management is not just a buzzword; it’s a cornerstone of success for modern businesses. This section delves deep into organizations that stand out for their outstanding quality management practices. These companies demonstrate a commitment to quality that goes beyond mere compliance to regulations; they embed quality into their corporate DNA. By analyzing their approaches, readers can glean techniques and insights applicable to a range of industries and sectors.
One of the key elements of quality management is continuous improvement. Companies that exemplify exceptional practices understand that in today’s fast-paced environment, standing still is not an option. They constantly refine their processes, enhance productivity, and strive to exceed customer expectations. This not only benefits internal operations but also creates loyal customers who are more likely to advocate for the brand.
Another consideration is the role of leadership in promoting a quality culture. These organizations often feature strong leadership that prioritizes quality at every level. Leaders create frameworks where all employees feel empowered to contribute to quality initiatives. More than just directives, these leaders instill values and encourage a shared vision which ultimately fosters a sense of ownership amongst staff members.
The importance of company culture cannot be overstated. Organizations like Toyota, Elia Group, and Procter & Gamble have rooted their quality management strategies in cultural ethos that goes beyond policies and procedures. Their practices inspire employees to take pride in their work, resulting in enhanced performance and accountability.
"Quality means doing it right when no one is looking." - Henry Ford
In the sections that follow, we will take a closer look at the outstanding quality management practices of specific companies. Each case study will highlight unique strategies and measurable outcomes, providing a rich database of best practices in quality management.
Case Study: Toyota
Principles of Lean Manufacturing
At the core of Toyota’s approach is the Principles of Lean Manufacturing, which emphasizes efficiency by eliminating waste without sacrificing productivity. This principle isn’t just a method; it’s a way of thinking that permeates through all levels of the organization, making operational excellence an everyday practice.
One of the key characteristics of lean manufacturing is its insistence on continuous value delivery to customers. By streamlining processes and focusing on what truly adds value, Toyota increases throughput while minimizing excess. The unique feature here is the just-in-time system, which aligns production schedules with customer demand. However, it does present risks in situations of supply chain disruption, as the reliance on timely deliveries can be somewhat precarious.
Continuous Improvement Culture
Toyota also nurtures a Continuous Improvement Culture, known locally as Kaizen. This culture encourages all employees to look for small ways to improve their work everyday. Not only does this drive higher efficiency, but it also helps to cultivate a sense of belonging among workers.
A powerful aspect of this culture is its grassroots nature. Rather than top-down mandates, suggestions for improvements can come from the assembly line workers themselves, making it a collaborative pursuit. It generates a sense of ownership and accountability, although it requires significant commitment and training that can be resource-intensive.
Case Study: Elia Group
Regulatory Compliance and Quality Assurance
The Regulatory Compliance and Quality Assurance practices at Elia Group are structured to meet both legal requirements and internal quality standards. This ensures not only adherence to regulations but also a commitment to the highest level of service delivery in energy management.
A vital aspect of these practices is how they promote transparency, both internally and externally. By maintaining a rigorous compliance framework, Elia fosters trust among stakeholders. However, the complexity and cost of compliance can sometimes be a challenge, requiring continuous resource allocation and training.
Stakeholder Engagement Strategies
Elia Group also implements robust Stakeholder Engagement Strategies. This involves actively involving customers, employees, and regulators in the decision-making processes that affect quality. Such engagement leads to richer feedback loops and allows the company to adapt swiftly to changing needs.
A key characteristic of these strategies is their focus on building relationships built on mutual respect and understanding. This level of engagement not just enhances quality but also creates a loyal customer base. However, getting stakeholders truly invested can be a strenuous task, which leads to potential inconsistencies depending on stakeholder commitment.
Case Study: Procter & Gamble
Consumer-Centric Innovations
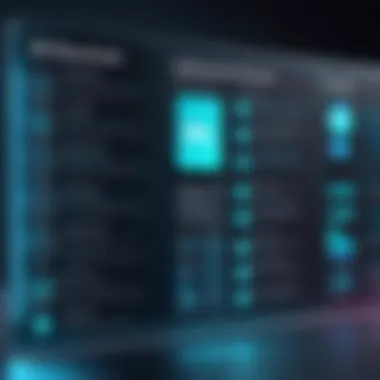
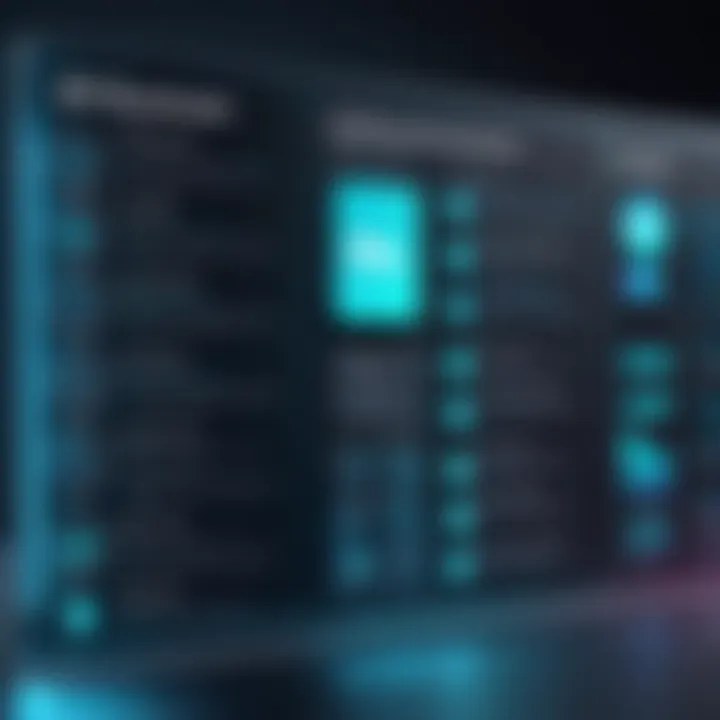
Procter & Gamble’s approach to Consumer-Centric Innovations showcases how a focus on the consumer can drive product excellence and market success. The company routinely leverages consumer insights to guide product development, creating something that truly resonates with users.
The unique feature of this approach is its application of design thinking, where every new product is conceived with the end-user in mind, ensuring relevance in ever-changing market dynamics. While this responsiveness to consumer feedback enhances loyalty and satisfaction, it can also lead to shifts in strategy that require constant adaptation, which may strain resources.
Global Quality Strategies
Procter & Gamble’s Global Quality Strategies reflect its ambition to standardize exceptional quality across all markets while respecting local preferences. The focus here is on consistent product quality no matter where it is produced or sold.
An important aspect of this is their strict quality control measures enforced at every stage of production. This ensures a level of reliability that consumers expect and trust. However, the global nature of these strategies means P&G must navigate different regulatory environments, which can complicate operations and increase costs.
Challenges in Quality Management
Understanding the challenges in quality management is crucial for organizations striving for excellence. The journey toward the apex of quality is fraught with obstacles that can hinder progress. Recognizing these challenges helps professionals implement strategies that not only improve quality but also foster a culture of continuous improvement.
Resistance to Change
Change is necessary for improvement, yet it often faces pushback from employees at various levels. People tend to feel more comfortable with the status quo. A shift towards quality management practices may be perceived as an unwelcome disruption. This resistance can arise from several factors:
- Fear of the unknown: Employees may worry about how changes will affect their job roles.
- Lack of training: Without proper guidance, employees might feel unequipped to adapt to new processes or systems.
- Miscommunication: If the rationale behind changes isn't clearly communicated, staff might feel skeptical or uninformed.
Overcoming this resistance requires careful strategy. Leaders must engage employees in considering quality initiatives, inviting their input to create a sense of ownership. Recognizing their contributions and addressing concerns directly can also smooth the transition. Times of change need effective communication—keeping everyone in the loop reduces hesitation and builds trust.
Balancing Cost and Quality
Cost pressures often lead to compromises in quality management. Organizations face the daunting task of balancing cost-effectiveness with maintaining high standards of quality. Stakeholders frequently push to minimize expenses, making it tempting to cut corners. However, this approach can have far-reaching implications:
- Customer satisfaction: Quality issues often result in unhappy customers and can tarnish a brand's reputation.
- Long-term costs: Poor quality can lead to increased returns, repairs, and customer support, ultimately costing more than any short-term savings.
Finding this balance isn't merely about cutting costs; it's about integrating quality into the manufacturing or service processes from the start. While initial investments may seem hefty, the return typically manifests in enhanced customer loyalty, reduced waste, and stronger overall financial health.
Maintaining Consistent Standards
Quality management is not a one-and-done effort; it represents a continuous endeavor. Organizations face the challenge of maintaining consistent quality across all products or services. Variations can stem from:
- Employee turnover: New hires may not possess the same level of training or familiarity with quality standards.
- Supplier variability: Dependable suppliers ensure consistency, but switching sources can introduce discrepancies.
- System shortcomings: Lack of established procedures often results in variable outcomes.
To combat this challenge, rigorous training programs for both new and existing employees can help. Moreover, establishing standardized operating procedures to guide all processes is critical in achieving and sustaining quality benchmarks.
"Quality is never an accident; it is always the result of intelligent effort."
- John Ruskin
Future Trends in Quality Management
Quality management is constantly evolving, and keeping an eye on future trends is essential for organizations looking to maintain a competitive edge. Understanding these emerging trends allows companies to adapt their strategies effectively, ensuring continuous improvement in their quality management practices. The significance of future trends in quality management stems from the integration of innovative technologies and sustainable practices that shape the operational landscape. As we look forward, companies are increasingly driven by data analytics, automation, and a pressing need for environmentally friendly practices.
Technology's Role in Quality Management
In today's fast-paced business environment, technology plays a pivotal role in elevating quality management efforts. From advanced data analytics to the Internet of Things (IoT), organizations leverage these tools to not only monitor but also optimize their quality performance.
By implementing software that tracks product quality in real time, companies can identify issues much earlier in the production process, reducing waste and enhancing customer satisfaction. For instance, a manufacturing company might use sensors that provide live updates about machinery performance, thus allowing managers to make informed decisions that eliminate downtime.
"Embracing technology in quality management is no longer optional. It's a necessity that separates the wheat from the chaff."
Additionally, Artificial Intelligence (AI) is enabling organizations to analyze vast amounts of data, uncovering trends that might not be immediately apparent. With predictive analytics, businesses can forecast potential quality issues before they escalate, paving the way for proactive measures rather than reactive fixes. This shift towards predictive quality management highlights a fundamental transformation in the approach to maintaining standards—moving from inspection to prevention.
Integrating Sustainability Practices
As companies begin to recognize the importance of sustainability in their operations, integrating environmentally conscious practices into quality management frameworks is becoming increasingly essential. The modern consumer prioritizes sustainability, and businesses that neglect this aspect might find themselves on shaky ground.
Adopting sustainable practices doesn't just enhance a company's reputation; it often leads to improved efficiency and reduced costs in the long run. For instance, organizations can focus on reducing material waste, enhancing energy efficiency, and using sustainable resources in production.
Sustainable practices also resonate well with employees, as many prefer working for companies that align with their personal values. This alignment can enhance employee engagement and morale—key ingredients in fostering a culture of quality improvement.
In summary, future trends in quality management present both challenges and opportunities. Companies that embrace technology and sustainability will not just keep pace with today’s competitive landscape but also position themselves for success in an increasingly conscientious marketplace.
Finale and Key Takeaways
In wrapping up our exploration of exceptional quality management practices, it's crucial to pinpoint the significant insights gleaned from our discussions. These insights not only highlight the stellar examples set by companies like Toyota, Elia Group, and Procter & Gamble but also tie back to overarching principles that govern successful quality management approaches.
Summarizing Key Points
Quality management isn't just a tick-box exercise; it integrates deeply into the core of a business's strategy. Below are vital points to take away from this article:
- Understanding Quality Management: It's not merely about maintaining standards. It’s about a continuous pursuit of improvement, driven by customer feedback and stakeholder engagement.
- Leadership's Role: Every journey towards quality enhancement starts at the top. Leaders need to foster an environment that prioritizes quality and encourages input from all levels of the organization.
- Employee Engagement: A company blooms from the efforts of its people. Involving employees in quality discussions fuels a culture of ownership and accountability.
- Adoption of Methodologies: Frameworks like Lean Management and Six Sigma serve as roadmaps, guiding firms toward operational efficiency while minimizing waste.
- Measuring Performance: Regular tracking and assessment of quality management initiatives ensure that they're effective and aligned with business goals.
These aspects are instrumental in aligning an organization with its goals and enhancing its competitive edge in the marketplace.
Implications for Businesses
The implications of adopting robust quality management practices resonate across all domains of business. Not just for industry giants, these practices are applicable to small and medium-sized enterprises as well. Consider a few implications:
- Enhanced Customer Satisfaction: Companies that prioritize quality tend to deliver products and services that more closely meet customer expectations, thereby increasing loyalty and retention.
- Operational Efficiency: Businesses that employ systemic quality practices often discover leaner operations, as processes are refined and waste is systematically eliminated.
- Market Reputation: A strong commitment to quality fosters a positive organizational reputation, setting the stage for competitive advantages.
- Regulatory Compliance: For industries that are heavily regulated, a solid quality management system not only guarantees adherence to standards but also minimizes the risk of non-compliance penalties.
Implementing these methods can act as a catalyst for growth, propelling businesses toward sustainable success. By absorbing the lessons from leading companies and adapting them, any organization can better its quality practices and performance.