Best Manufacturing Execution Software Guide
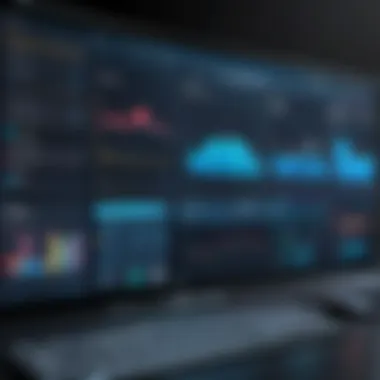
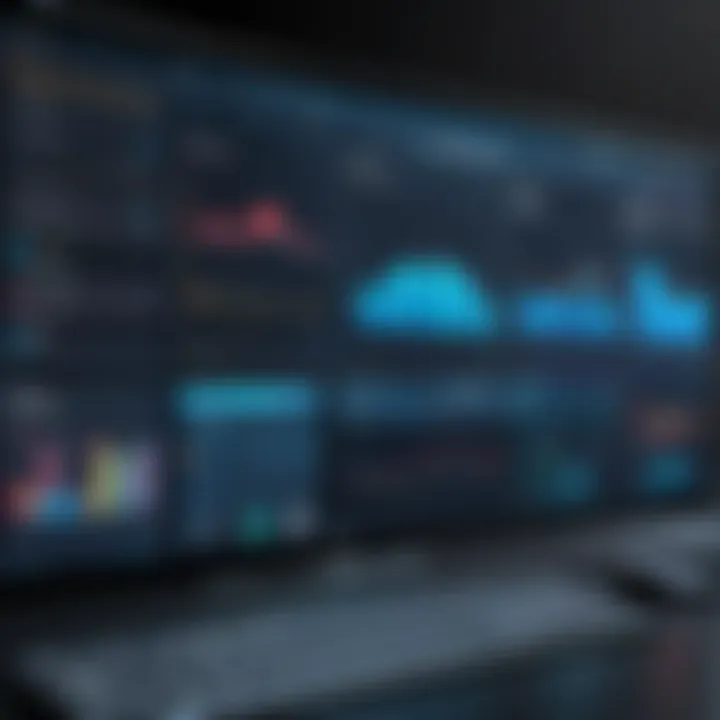
Intro
In the rapidly evolving landscape of manufacturing, businesses face a multitude of challenges. Efficient production processes are no longer optional; they are essential for survival and growth in a competitive market. To address these challenges, manufacturing execution software (MES) has emerged as a critical tool. This guide delves into the best manufacturing execution software available today, examining key functionalities, features, and comparative advantages. The aim is to provide insights to business professionals and technology enthusiasts alike.
MES solutions enable manufacturers to enhance productivity, streamline operations, and drive competitive advantage. These systems bridge the gap between enterprise operations and production, ensuring real-time data flow and visibility. This guide also explores the challenges firms encounter in implementing such software, offering valuable considerations and strategies for success.
By the end of this guide, readers will discern the top software options in the market, the unique features they offer, and the pivotal factors to consider during the selection process. Whether you are an IT professional, a software specialist, or a business leader, the insights shared here will assist in making informed choices around manufacturing execution systems.
Preface to Manufacturing Execution Software
In the current climate of industrial and technological advancement, understanding Manufacturing Execution Software (MES) is critical for enhancing operational effectiveness within any manufacturing unit. As systems become more interconnected, the role of MES evolves into a crucial component that can significantly influence a company's productivity, quality control, and overall efficiency. This software acts as a bridge between physical manufacturing processes and enterprise resource planning, providing real-time data that facilitates informed decision-making.
The relevance of MES goes beyond mere production tracking. In an age where efficiency can dictate market success, companies are increasingly looking towards robust solutions to optimize their operations. Key benefits of employing manufacturing execution software include streamlined workflows, better visibility across production processes, and improved communication among stakeholders.
Moreover, as manufacturing environments grow in complexity, the need for tools that offer real-time feedback and analytics becomes even more pressing. Selecting an appropriate MES solution is not purely about addressing current operational challenges; it is also about future-proofing the business against ongoing evolutions in the manufacturing sector.
Understanding the importance of MES is foundational before diving into its nuanced features and benefits. By assessing specific company needs aligned with the functionalities these software solutions offer, businesses can formulate strategies that enhance their competitive edge.
Defining Manufacturing Execution Software
Manufacturing Execution Software refers to a suite of applications designed to manage and optimize manufacturing processes. It serves as a comprehensive platform that monitors production in real-time, ensuring that operations align with the planned schedules and quality standards. In essence, MES provides actionable insights into every aspect of the manufacturing operation, from raw material input to product output.
Some key defining characteristics of MES include:
- Real-Time Data Acquisition: Collects data from various points within the production line, allowing for immediate assessments of performance and quality.
- Process Control: Facilitates adjustments to manufacturing processes based on real-time feedback, improving overall output.
- Reporting and Analytics: Generates reports that help in understanding performance metrics, facilitating the identification of areas for improvement.
In summary, MES encapsulates tools that enhance visibility and control over the production process, fostering a data-driven culture in manufacturing environments.
Brief History and Evolution
The development of Manufacturing Execution Software can be traced back to the late 20th century when manufacturers began recognizing the need for efficient real-time monitoring systems. Initially, these systems were limited in scope and functionality, focusing primarily on data collection and reporting. Over time, advancements in technology and the increasing complexities of manufacturing processes drove significant innovations in MES.
From simple batch tracking tools, MES evolved into comprehensive platforms that integrate seamlessly with other enterprise systems. The introduction of modern technologies like the Internet of Things (IoT), artificial intelligence, and cloud computing further revolutionized how MES operates.
Some notable milestones in the evolution of MES include:
- 1990s: Early adoption of computer-aided manufacturing systems.
- 2000s: Integration of MES with other enterprise systems like ERP and SCM for holistic management.
- 2010s: Incorporation of IoT and data analytics, enabling predictive capabilities and advanced process optimization.
Today, MES is not just about monitoring production but encompasses strategic planning, quality assurance, and overall supply chain visibility. As manufacturing continues its digital transformation, understanding the history of MES helps contextualize its current capabilities and future potential.
Importance of Manufacturing Execution Systems
Manufacturing execution systems (MES) hold a critical role in modern production environments. Their impact can extend from the factory floor to the bottom line of a business. As industries move towards greater automation and data integration, the value of MES becomes apparent in maintaining operational efficiency both in small and large businesses.
Operational Efficiency
One of the primary benefits of manufacturing execution systems is enhancing operational efficiency. MES streamline production processes by providing a real-time view of operations. By monitoring every aspect of manufacturing, these systems help to identify bottlenecks and areas for improvement quickly. When processes are more efficient, companies can reduce cycle times and lower costs.
- Resource Utilization: MES optimize the use of machines, labor, and materials. This ensures that resources are not wasted, contributing to higher productivity.
- Workflow Automation: By automating routine tasks, MES reduce manual input and the potential for human error. This fosters a more reliable workflow.
In summary, operational efficiency is not just about speed; it is about maximizing resource use and minimizing delays which leads to improved outcomes for businesses.
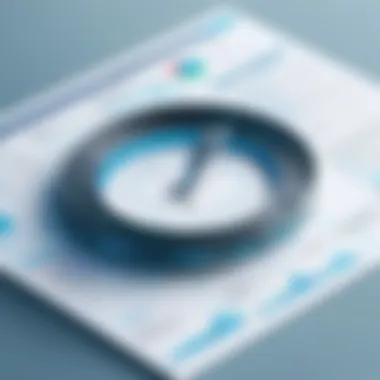
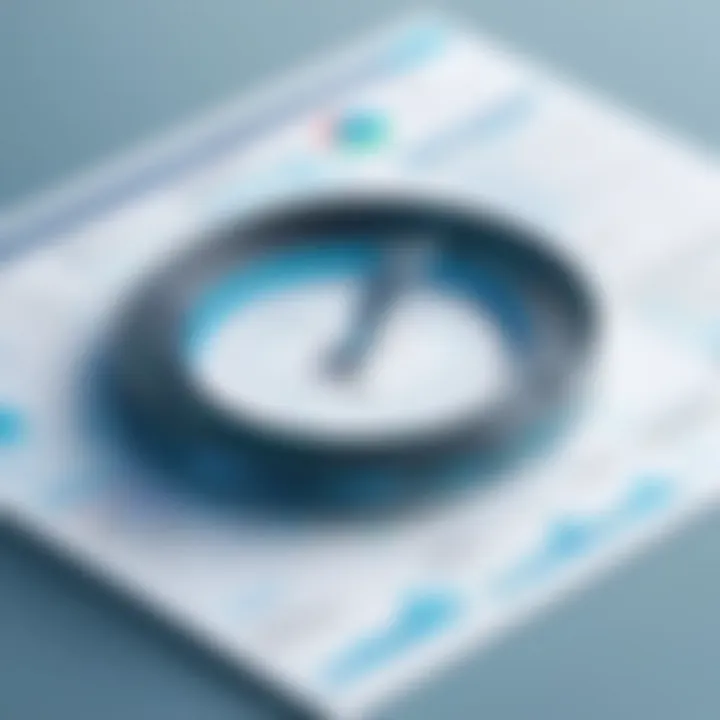
Real-time Tracking and Reporting
Real-time tracking is another significant aspect of manufacturing execution systems. This feature allows companies to monitor their processes at any moment. When using MES, production managers can observe progress on the floor without delay. This immediacy leads to better decision-making, as potential issues can be addressed before they escalate.
- Immediate Access to Data: Managers have instant access to performance metrics through dashboards. They can evaluate productivity levels, machine status, and staff output, allowing for informed decisions.
- Enhanced Communication: Real-time data supports better communication among teams. Everyone stays informed about production status, which helps to align efforts across departments.
Ultimately, real-time tracking and reporting contribute to a transparent production environment, facilitating quicker and actionable insights.
Quality Management
Quality management is essential for any manufacturing process, and MES helps to ensure that standards are met consistently. By integrating quality assurance within the production process, these systems help prevent defects and ensure product conformity.
- Continuous Monitoring: MES can monitor operations for quality control. This assists in identifying defects early, allowing for corrective measures that prevent a larger scale of waste or recalls.
- Data-Driven Decisions: By collecting data related to quality metrics, businesses can analyze trends over time. This information is valuable for implementing process improvements.
In summary, effective quality management with the support of manufacturing execution systems fosters customer satisfaction and brand loyalty.
Key Features of Top Manufacturing Execution Software
Understanding the key features of manufacturing execution software is crucial for any organization aiming to boost productivity and streamline operations. These features are the building blocks that determine how well the software will function in a real-world manufacturing environment. The right capabilities can lead to improved operational flow, making it essential to examine each feature carefully.
Production Planning and Scheduling
One of the primary functions of manufacturing execution software is production planning and scheduling. Effective scheduling ensures that resources are allocated efficiently, reducing downtime and maximizing output. This feature allows businesses to plan production runs based on demand forecasts, helping to balance workloads across different machines and teams.
Another important aspect is the real-time capabilities. With live data updates, businesses can adjust schedules on-the-fly in response to unforeseen circumstances like equipment failures or supply chain delays. This agility is essential for maintaining productivity. Moreover, the software can help predict lead times, letting teams know when to expect materials and what timeline is realistic for finishing products.
Work Order Management
Work order management is essential for tracking jobs through the production process. This feature allows employees to view and manage tasks directly related to specific orders. A well-designed work order management system will integrate with inventory levels, ensuring that necessary materials are available when needed. It can also send alerts if certain thresholds are hit, allowing for proactive management of resources.
In addition, this management tool provides visibility into job progress, allowing supervisors to monitor efficiency and identify bottlenecks more easily. Workflow visualization, integrated into the software, enables teams to see where delays occur and make adjustments accordingly.
Performance Analytics
Another significant feature is performance analytics, which delivers crucial insights into various aspects of manufacturing operations. This feature helps track key performance indicators (KPIs) such as overall equipment effectiveness (OEE), production rates, and cycle times.
By analyzing this data, organizations can make informed decisions that enhance efficiency. For example, if a particular machine has consistent downtime, it may require maintenance or even replacement. Performance analytics therefore, acts as a tool for continuous improvement, enabling businesses to focus on areas that need attention to optimize overall processes.
Integration with Other Systems
The ability to integrate manufacturing execution software with other systems such as supply chain management, enterprise resource planning, and customer relationship management is another imperative feature. Integrations enhance the flow of information across all departments, ensuring that everyone has access to real-time data. This interconnectedness eliminates information silos and promotes a more cohesive operational framework.
Furthermore, seamless integration also allows for advanced analytics, where data from various sources can be combined to offer comprehensive insights. For instance, aligning sales forecasts with production scheduling can lead to greater alignment between what is produced and what is sold.
Evaluating Manufacturing Execution Software
Evaluating manufacturing execution software is a crucial step that can define how well a business can optimize its processes. With the right software, organizations can achieve higher operational efficiency and improve overall productivity. This evaluation includes a comprehensive look at factors such as organizational needs, associated costs, and vendor support.
Assessing Business Needs
Before selecting any manufacturing execution software, assessing business needs is essential. Each organization has unique processes and challenges. Thus, understanding specific requirements can guide the software selection process. Here are some points to consider:
- Scope of Operations: What level of detail does your operation need? Some businesses may require software that offers detailed tracking of production lines, while others may need a broader overview.
- Integration Requirements: Consider how well the new software will integrate with existing systems. Lack of integration can lead to data silos or inefficiencies.
- User Demand: Understanding the number of users and their roles can help in selecting scalable software. An organization with many users may need a solution that can handle multiple logins seamlessly.
- Regulatory Compliance: Certain industries have strict compliance measures. Ensure the software has features that support adherence to these regulations.
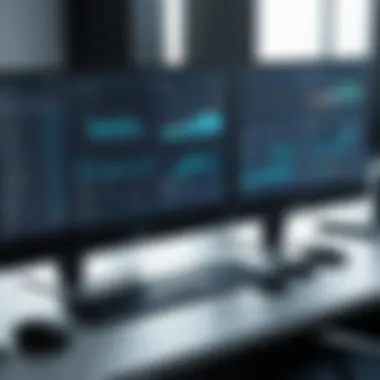
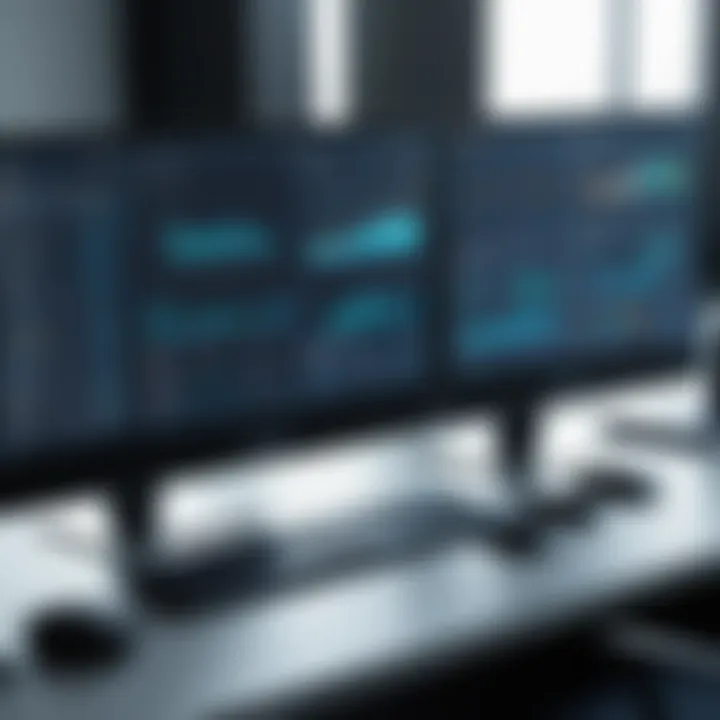
Cost Considerations
Cost is another vital factor in evaluating manufacturing execution software. Organizations must balance functionality with budget constraints. Several cost-related factors include:
- Initial Investment: Look at the upfront cost of purchasing the software. This may include licenses and installation fees.
- Maintenance Costs: Regular updates and support can add to the total cost. Understanding how vendors charge for ongoing maintenance is necessary.
- Training Expenses: Employees may require training to effectively use the new software. Factor in these costs as part of the total investment.
- Hidden Costs: Some software solutions may have hidden fees, such as charges for additional users or modules. Thoroughly review contracts and pricing models to avoid surprises.
Vendor Reputation and Support
Choosing a vendor with a solid reputation can significantly impact the software's success in your organization. Here are elements to examine when considering vendor reputation and support:
- Customer Reviews: Researching reviews from other businesses can provide insights into the vendor's reliability. Websites and platforms, such as Reddit and Facebook, often have user feedback that can shed light on real-world experiences.
- Support Claims: Assess the vendor's support offerings. Are they responsive? Do they provide training and resources? Quality support can make a difference when issues arise.
- Track Record: Evaluate the vendor's history in the industry. A company with years of experience may have more robust solutions and better customer service.
- Scalability Options: Consider if the vendor can accommodate future growth. As your business evolves, the software should adapt to changing needs.
"Selecting the right manufacturing execution software is not just about technology; it's about matching the solution to the strategic goals of the organization."
In summary, evaluating manufacturing execution software involves careful assessment of business needs, cost implications, and vendor reputation. Making measured choices in these areas not only enhances operational efficiency but also aligns software capabilities with strategic objectives.
Top Manufacturing Execution Software Solutions
The selection of suitable manufacturing execution software solutions plays a critical role in achieving operational success. The software directly integrates with production processes, offering tools for planning, monitoring, and analysis. This ensures businesses can respond to market demands effectively while maintaining quality and compliance. As the landscape evolves, identifying the most reliable options becomes essential for leveraging technological advancements in manufacturing.
Software A: Features and Benefits
Software A is one of the frontrunners in the manufacturing execution software market. It provides significant capabilities that address various needs in production environments. Key features include:
- Real-Time Monitoring: This allows managers to see live data on production processes. It enables swift corrections and adjustments that can impact efficiency.
- Quality Control Tools: Integrated quality checks ensure that production meets desired standards, thus minimizing waste and reducing rework.
- User-Friendly Interface: The system is designed to facilitate easy navigation, which reduces training time for employees.
The benefits derived from Software A include improved communication through centralized data, faster decision-making, and increased overall productivity.
Software B: Features and Benefits
Software B stands out for its robust analytics capabilities. It offers tools that help manufacturers analyze production trends and performance metrics easily. Important aspects to note include:
- Predictive Analytics: Predictive models help anticipate equipment failures and maintenance needs.
- Customization: The software allows customization of dashboards, enabling users to tailor the interface to specific needs and preferences.
- Integration Options: This software can integrate with ERP systems, enhancing data flow across business functions.
The strengths of leveraging Software B lie in its ability to enhance strategic decision-making. Companies can refine their processes and adapt to changing demands by utilizing data-driven insights.
Software C: Features and Benefits
A different approach comes with Software C, which focuses on scalability. Its ability to cater to both small and large businesses makes it versatile. Essential features include:
- Scalable Architecture: It adjusts for growing business needs, ensuring that companies from various sizes can adopt it without changing platforms as they expand.
- Multi-Site Capability: Allows centralized monitoring of production across multiple locations.
- Mobile Access: Offers mobile functionalities, permitting management to monitor operations remotely.
The notable advantage of Software C is its flexibility. Organizations can implement it without risking disruption during scaling efforts.
Software D: Features and Benefits
Software D is known for its exceptional support and training options. These features significantly reduce implementation times and hurdles faced during onboarding. Key features include:
- Comprehensive Training Resources: It provides extensive resources to train staff effectively, ensuring quick adaptation.
- 24/7 Support: Continuous support helps businesses resolve issues swiftly, reducing downtime.
- Webhook Capabilities: Effective for integration with third-party tools and applications, which enriches its functionality.
By opting for Software D, businesses gain a partner that prioritizes support and customer service. This contributes to overall satisfaction and smooth operational transitions.
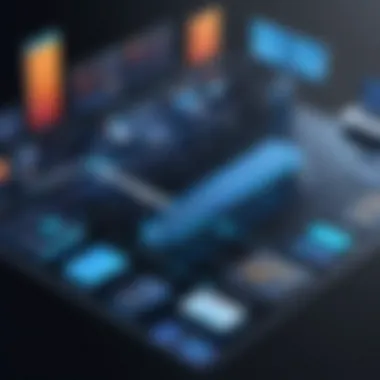
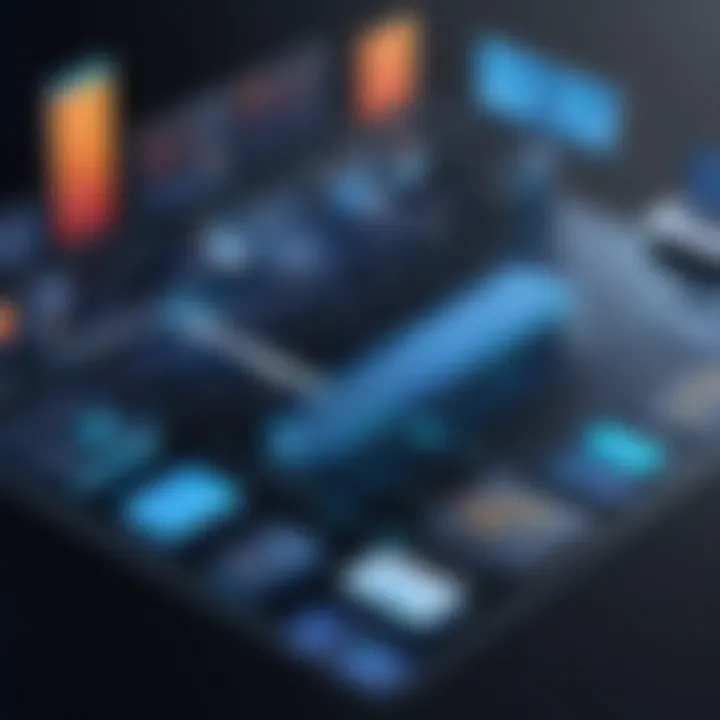
Challenges in Implementing Manufacturing Execution Software
The implementation of manufacturing execution software is not just a technical exercise. It involves significant change management, cultural adjustments, and practical considerations that can pose hurdles. Recognizing these challenges is essential for a successful transition. Failure to address them can lead to delays, increased costs, and even technology failures. Therefore, it is crucial to understand the factors that might hinder smooth implementations such as resistance to change and concerns over data security.
Resistance to Change
Resistance to change is a common phenomenon in many organizational settings. Employees often feel apprehensive about adopting new technologies, fearing that it might disrupt their routines or threaten their job security. In manufacturing settings, where workflows are usually well-established, the introduction of new execution software can be met with skepticism. This resistance can be compounded when employees do not perceive immediate benefits from the new system.
To mitigate this, organizations should prioritize effective communication. Engaging employees early in the process can foster a sense of ownership and ease anxieties about new software. Training sessions to familiarize staff with the software can also enhance confidence. This approach encourages them to view the technology as a tool that can simplify their tasks rather than complicate them. Moreover, it is valuable to outline the specific benefitsโsuch as better monitoring of production lines and reduction of manual errorsโthat the new system can bring to their daily work.
Data Security Concerns
Another significant issue in the implementation of manufacturing execution software is data security. As organizations increasingly rely on digital systems, the management of sensitive information becomes paramount. Manufacturing systems often handle proprietary information, customer data, and operational metrics. Any breach could not only harm the organization financially but also damage its reputation.
To counter these concerns, manufacturers must ensure that their software solutions come equipped with robust security features. This includes encryption protocols, regular software updates, and stringent access controls. In addition, companies should invest in training for their employees on best practices for data handling and cybersecurity. Developing a culture of security awareness can go a long way in safeguarding sensitive information, which is essential for maintaining trust with clients and partners.
Important Note: Adopting a proactive approach to handling resistance and security issues is vital for the successful deployment of manufacturing execution software. Organizations can increase acceptance and safeguard crucial data when they address these challenges head-on.
The Future of Manufacturing Execution Software
The future of manufacturing execution software (MES) is poised for significant transformation. As industries continue to adapt to rapid changes in technology and market demands, MES systems must evolve as well. This section explores the pivotal elements shaping the future of these systems. Understanding these trends allows businesses to leverage potential advantages and anticipate challenges ahead.
Emerging Technologies Impact
Emerging technologies are redefining manufacturing landscapes. The incorporation of artificial intelligence (AI), machine learning, and the Internet of Things (IoT) is becoming more common in MES solutions. These technologies enable real-time data analysis and automation, offering businesses enhanced capabilities.
- Artificial Intelligence: AI can analyze vast amounts of data to provide actionable insights, improving decision-making processes.
- Machine Learning: Systems can adapt and improve based on past experiences, allowing for predictive maintenance and optimization of operations.
- Internet of Things: IoT devices enhance connectivity between machines, enabling seamless data flow and better operational visibility.
As these technologies integrate into MES, the systems will become more intelligent, offering data-driven recommendations and improved user interfaces. These advancements represent not just trends but essential components for companies striving to maintain competitiveness.
Sustainability Trends
Sustainability is becoming a non-negotiable aspect for manufacturers. Environmental concerns and regulatory pressures are driving the need for sustainable practices in operations. MES systems play a crucial role in this transition by facilitating efficient resource management and process optimization.
- Waste Reduction: Advanced MES can track material usage in real-time, minimizing waste and promoting recycling initiatives.
- Energy Efficiency: By monitoring energy consumption, manufacturers can identify inefficiencies and implement energy-saving strategies.
- Supply Chain Transparency: MES systems support ethical sourcing and sustainability by providing visibility along the supply chain.
"Sustainable practices in manufacturing will ensure long-term viability and compliance in a changing regulatory landscape."
Adopting sustainability-focused features in MES not only helps comply with regulations but also improves brand reputation and customer loyalty. As customers increasingly favor companies committed to sustainable practices, the influence of these trends on the future of MES cannot be understated.
Culmination
In the context of this article, the conclusion serves as a crucial synthesis of the discussed elements related to manufacturing execution software. The insights provided throughout highlight the importance of understanding both the software solutions available today and the operational challenges faced by manufacturers. Selecting the right manufacturing execution software can significantly affect overall productivity and efficiency within a business. It is not merely about choosing software, but rather about making a strategic decision that aligns with the goals and operational needs of the organization.
Recap of Key Insights
Key insights from this comprehensive guide have focused on several pivotal areas. We explored the defining features of manufacturing execution software, the various advantages they offer, and the criteria for evaluating them effectively.
- Operational Efficiency: Efficiency gains are paramount, as manufacturing execution software allows for better tracking of production metrics.
- Real-time Tracking and Reporting: Access to data in real-time fuels informed decision-making, ensuring that manufacturing processes adapt swiftly to any changes or challenges.
- Integration Capabilities: The ability to integrate seamlessly with existing systems is essential for maximizing the benefits of new software solutions.
- Future Trends: Awareness of emerging technologies and sustainability trends provide a lens through which organizations can prepare for future demands.
These insights collectively underline that the path to an effective manufacturing execution system is paved with a thorough understanding of both software capabilities and organizational requirements.
Final Thoughts on Software Selection
The process of selecting manufacturing execution software demands careful consideration. It is crucial for decision-makers to evaluate their specific business needs, budget constraints, and the reputation of vendors in the market.
- Assess Business Needs: Organizations must identify their unique operational challenges to select software that addresses these effectively.
- Cost Considerations: A comprehensive cost-benefit analysis will ensure that investments yield tangible returns.
- Vendor Support: In addition to features, the level of support and training provided by vendors is vital for successful implementation and long-term usage.
In summary, choosing manufacturing execution software is a strategic undertaking that should not be rushed. By reflecting on the key insights and considerations outlined in this article, businesses can make informed decisions that enhance operational efficiency and competitiveness.